تکنیک "۵ چرا" روشی آسان برای کشف علت ریشهای مشکلات است که بهطور گسترده در صنایع مختلف بهکار میرود. در این روش، مدیران و اپراتورها میتوانند با طرح ۵ پرسش مسائل را از زوایای مختلف بررسی و ارتباطات جدید میان پیامدها و علل اصلی مشکلات را شناسایی کنند، در حقیقت پاسخ به پرسش پنجم علت اصلی وقوع مشکلات را آشکار میکند.
از تکنیک ۵ چرا برای بهینهسازی فرایندها و بهبود کیفیت استفاده میشود؛ زیرا به تولیدکنندگان کمک میکند تا با تجزیهوتحلیل دادهها تصمیمات مهمی را اتخاذ کنند.
مثالی برای تکنیک ۵ چرا
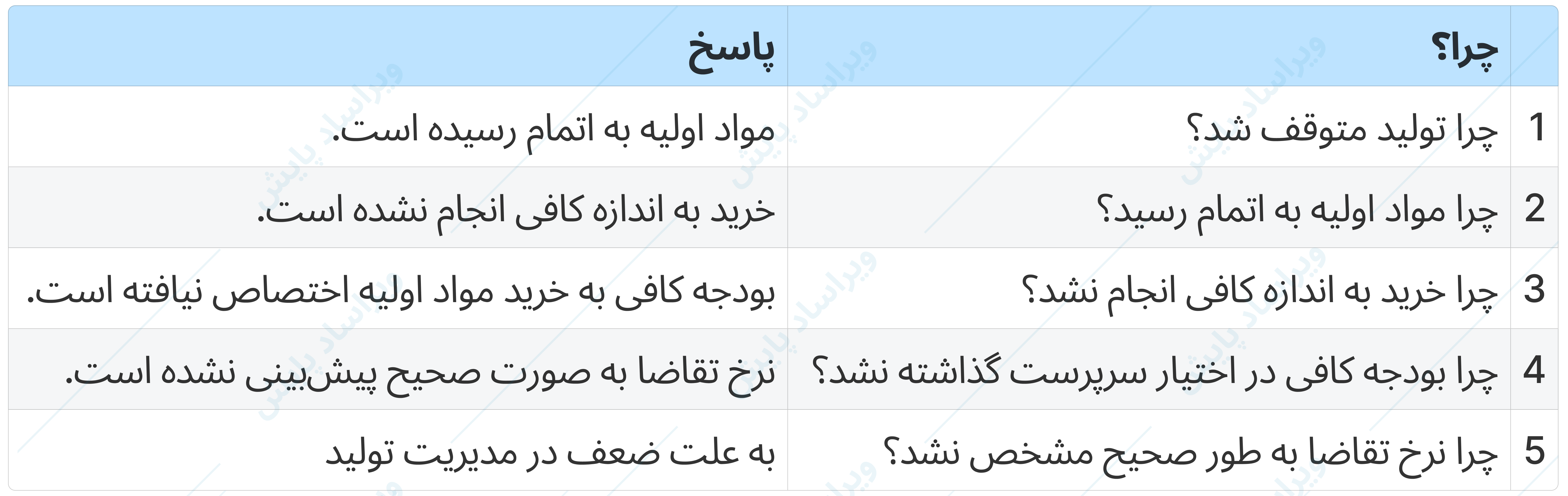
معضلات ناشی از عدم بهکارگیری تکنیک پنج چرا در صنعت
در این بخش به عواقب عدم استفاده از روش پنج چرا میپردازیم:
بیاطلاعی مدیران از فرایندهای جاری
وجود مشکلات صنعتی تولیدکنندگان را به فکر یافتن دلایل اصلی ایجاد مشکلات میاندازد. آنها همواره به دنبال شناسایی مشکلات موجود هستند؛ اما هرگز متوجه علل ریشهای مشکلات نخواهند شد و به دنبال آن متحمل پرداخت خسارات سنگین میشوند. این امر به معنای ضعف مدیریتی و نبود برنامهای منظم برای تولید است.
وجود ظرفیت پنهان در کارخانه
یکی دیگر از عواقب بیاطلاعی مدیران از نحوه انجام فرایندهای جاری، ایجاد ظرفیت پنهان در کارخانه و همچنین نادیدهگرفتن آن است. بهطورکلی عدم استفاده از تمام پتانسیل کارخانه و خط تولید به معنی کاهش ظرفیت تولید و ایجاد هزینههای گزاف میباشد. این در حالی است که روش پنج چرا به تولیدکنندگان کمک میکند تا با تعیین KPIهای دقیق، مشکلات را بهصورت ریشهای شناسایی و برطرف کنند.
تداوم در استفاده از مواد اولیه بیکیفیت
فرایند کنترل کیفیت مواد اولیه و سایر اقلام ورودی بر عهده کارشناسان کنترل کیفیت است. انجام صحیح این امر از اهمیت ویژهای برخوردار میباشد؛ زیرا ورود هرگونه مواد اولیه نامرغوب به خط تولید به منزله تولید محصولاتی بیکیفیت و در نتیجه تولید انبوهی از ضایعات است. از اینرو تولیدکنندگان میتوانند با طرح پنج پرسش کاربردی مانع از ساخت محصولات نامرغوب و معیوب شوند. از سویی دیگر این روش منجر به شناسایی تأمینکنندگان ضعیف و به دنبال آن قطع همکاری با آنها میشود.
اتلاف در تولید
اتلاف بلایی است که تمام صنایع به آن دچار میشوند و هیچ یک نمیتوانند از آن دور بمانند. این مشکل به شکلهای مختلفی اعم از هدررفت انرژی، اتلاف زمان، تولید ضایعات و هدررفت سرمایه نمایان میشود. بااینحال تولیدکنندگان میتوانند با استفاده از ابزارهای سودمند، بهکارگیری سایر روشهای تولید ناب و همچنین انجام اقدامات لازم میزان اتلاف را به حداقلترین حالت ممکن برسانند.
تعمیرات و نگهداری ضعیف
یکی از الزامات خط تولید تعمیر تجهیزات خراب و نگهداری تمام ماشینآلات در شرایط صحیح است؛ زیرا عدم رعایت فرایندهای تعمیر و نگهداری به معنی نادیدهگرفتن مشکلات و کاهش عمر تجهیزات صنعتی میشود. از اینرو تولیدکنندگان میتوانند بهمحض وقوع مشکل، ۵ پرسش لازم را طرح نموده و اصلیترین علت وقوع آن را شناسایی کنند.
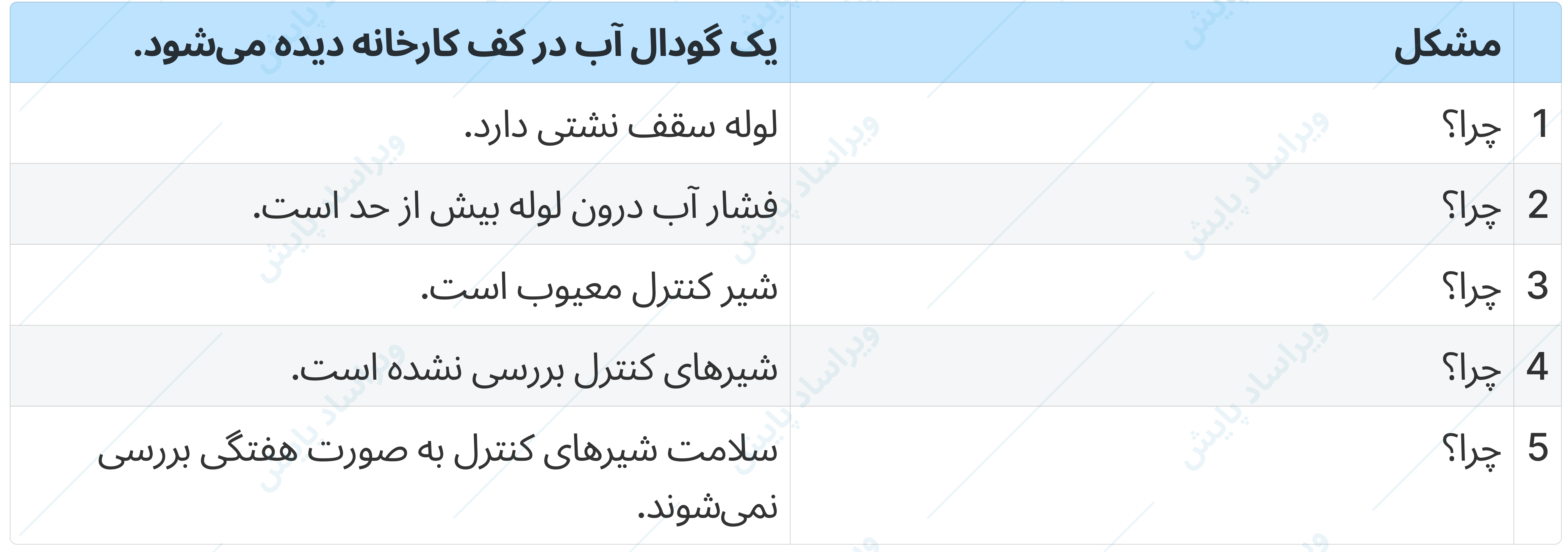
کاهش بهرهوری
مدیران همواره به دنبال افزایش بهرهوری کارخانه خود هستند؛ درحالیکه عوامل متعددی از جمله تولید محصولات بیکیفیت، هدررفت مداوم محصولات و مواد اولیه و همچنین تغییر مکرر تقاضای بازار به طور چشمگیری منجر به کاهش بهرهوری و به دنبال آن کاهش نرخ سوددهی کارخانه میشود. این در صورتی است که تکنیک ۵ چرا تولیدکنندگان را در جهت شناسایی و حل معضلات یاری میکند.
روش ۵ چرا برای حل مشکلات صنعتی
پنج چرا یکی از قویترین روشهای ارزیابی در بین تمام روشهای غیر آماری است که میتواند مشکلاتی را که بسیار واضح نبودهاند را کشف و ردیابی کند. تولیدکنندگان میتوانند از این روش بهمنظور حل مشکلات ساده و پیچیده و همچنین برطرف ساختن خطای انسانی استفاده کنند.
مزایای استفاده از تکنیک "۵ چرا" در تولید
بهکارگیری روش پنج چرا منجر به شناسایی مناطقی که تغییرات در آنها مؤثرتر هستند، میشود و در ادامه به بهبود فرایندهای تولید کمک میکند. در ادامه به مزایای کلیدی تکنیک 5why اشاره میکنیم:
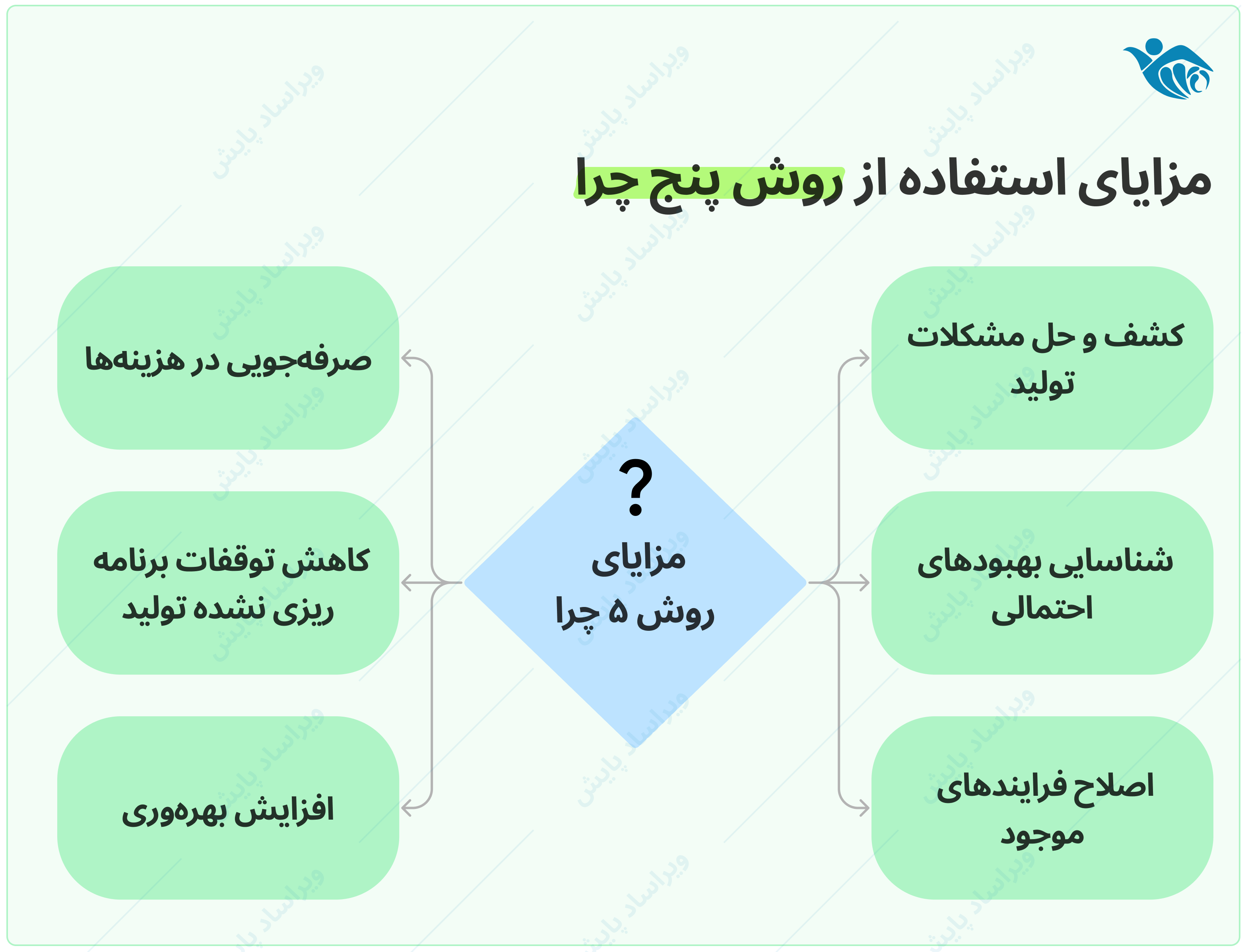
پیادهسازی روش 5 چرا در کارخانه
پیادهسازی روش 5why در سیستم تولید نیازمند یک رویکرد ساختاریافته است، بنابراین تولیدکنندگان میتوانند با اجرای مراحل زیر از مزایای این تکنیک در کارخانه خود بهرهمند شوند:
۱. شناسایی و تشریح یکی از بزرگترین مشکلات موجود در خط تولید
۲. طرح مکرر پرسش چرا؟ برای رسیدن به علت ریشه ای مشکل
۳. بررسی و اعتبارسنجی علت ریشهای مشکل بر اساس داده های تولید به کمک نرمافزار مدیریت تولید
۴. طراحی و اجرای اقدامات موثر بهمنظور برطرف ساختن علت ریشهای
۵. نظارت بر اجرای صحیح و نتایج حاصل از اقدامات اجرا شده
۶. تکرار این چرخه برای سایر مشکلات
ابزارهای پیادهسازی تکنیک ۵ چرا
سادهترین راه برای انجام تکنیک پنج چرا، نوشتن آن بر روی کاغذ است. البته این روش سنتی و زمانبر است و اطلاعات ثبت شده با این روش در پیگیری های بعدی به سختی قابل ردیابی هستند. از اینرو تولیدکنندگان میتوانند از روشها و ابزارهای جدیدتری بهمنظور شناسایی مشکلات تولید استفاده کنند، برخی از این ابزارها عبارتاند از:
نرمافزار نظارت بر تولید
نرمافزار نظارت بر تولید شامل مجموعه ابزارهایی است که از دادهها بهمنظور ردیابی، ثبت و تجزیهوتحلیل عملکرد ماشینآلات در زمان واقعی استفاده میکند. استفاده از این سیستم در کنار سختافزارهایی به منظور جمع آوری خودکار دادهها از طریق حسگرها، سیگنالهای ماشین آلات و سایر منابع وموجود در خط تولید، دادههای مهم بهصورت خودکار جمعآوری شده، سپس تفسیر و به اطلاعات مفید تبدیل میگردند. این امر طیف گستردهای از اطلاعات مؤثر در مورد فرایندها از جمله میزان تلفات، مقدار OEE و TEEP و KPIها را در اختیار مدیران و تولیدکنندگان میگذارد.
مشورت با کارشناسان صنعتی
گاهی اوقات ممکن است مدیران از سایر متخصصان برای شناسایی مشکلات و معرفی روشهای کاهش آنها مشورت بگیرند. از اینرو شما نیز میتوانید بهمنظور دریافت مشاوره رایگان با ما تماس بگیرید.