تولید ناب سیستمی است که با استفاده از ابزارهای کارآمد به کسبوکارهای کمک میکند تا ضایعات موجود را به حداقل برسانند و منجر به بهبود فرایندها شوند. رعایت اصول تولید ناب نه تنها سبب کاهش هزینههای تولید میشود؛ بلکه بهبود کیفیت محصولات تولیدی و افزایش توان رقابتی را نیز به همراه میآورد.
ابزارهای مهم در تولید ناب
حال بیایید به معرفی برخی از ابزارهای مهم در تولید ناب بپردازیم:
کانبان (KANBAN)
کانبان روشی برای مدیریت تولید ناب است که باهدف بهبود کارایی و تجسم گردش کار در بسیاری از سازمانها استفاده میشود. این سیستم با اولویتبندی و تقسیم وظایف سبب کاهش اتلاف زمان و هزینههای اضافی و همچنین مانع از بیکاری کارگران میشود؛ بنابراین به افزایش سود کسبوکارها کمک میکند. کانبان روشی است که با توجه به تقاضای مصرفکننده اجرا میشود، از اینرو احتمال ارتکاب اشتباه و تولید محصولات معیوب در این روش بسیار کمتر از سایر روشها است.
در روش کانبان از یک بورد ویژه بهمنظور نمایش فرایندهای در حال انجام استفاده میشود، مدیران میتوانند تغییرات موردنیاز را ثبت و میزان پیشرفت را اندازهگیری کنند.
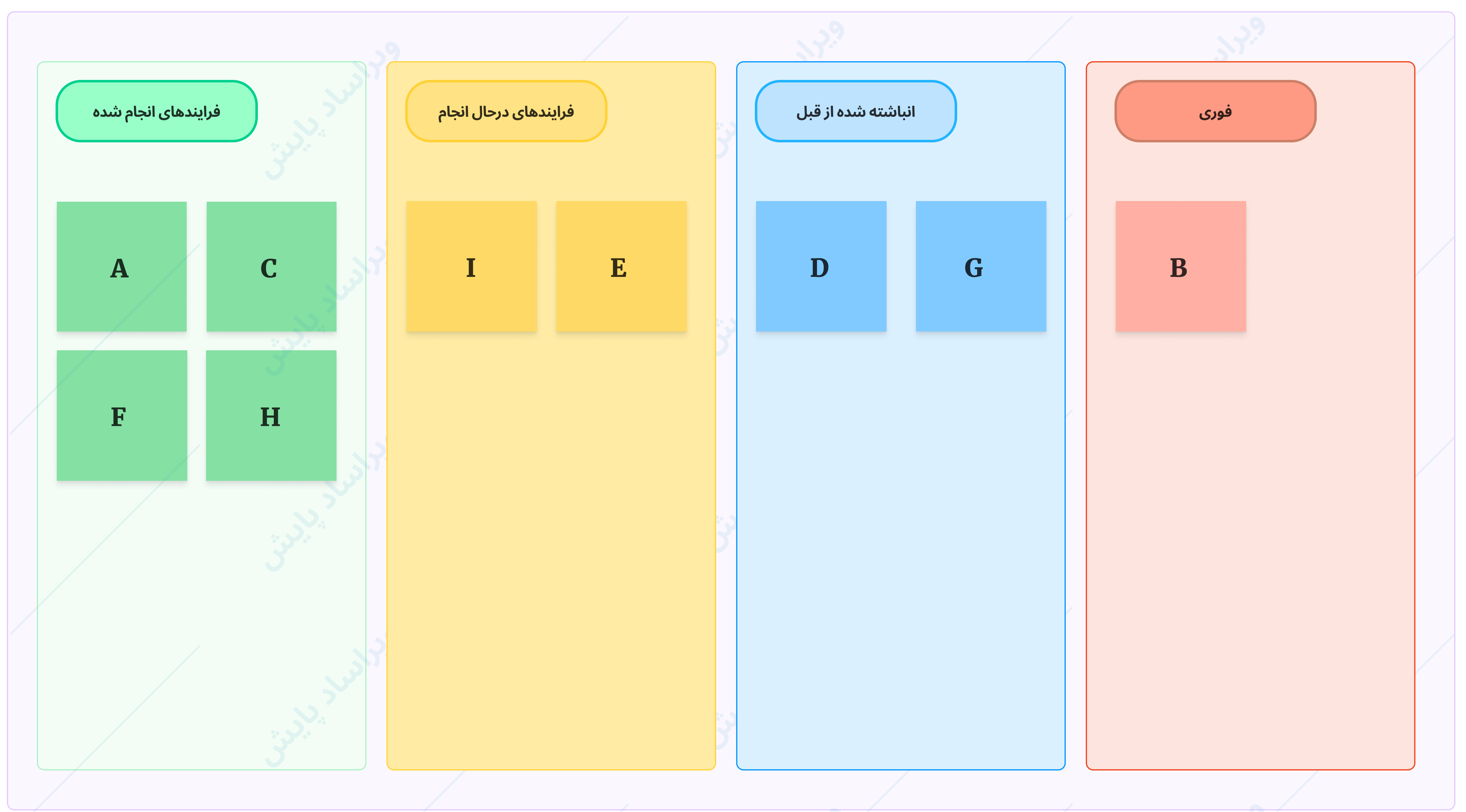
5S
5S روشی ناب برای بهینهسازی فضای کاری است . این سیستم با قابلیت اجرا در تمامی صنایع به مدیران اجازه میدهد تا با کاهش هزینههای تولید سبب افزایش کارایی و بهرهوری شوند. 5S از ۵ اصطلاح ژاپنی و مرتبط به هم تشکیل میشود:
Seiri (ساماندهی): دستهبندی ابزارها بهمنظور حذف تجهیزات و اقلام غیرضروری.
Seiton (نظم و ترتیب): طبقهبندی و قراردادن اقلام و وسایل ضروری در جای مناسب برای کاهش جابهجایی کارگران، کاهش اتلاف وقت و سهولت در استفاده از تجهیزات.
Seiso (پاکیزهسازی): پاکیزه نگهداشتن ایستگاههای کاری و ماشینآلات بهمنظور کاهش ضایعات و شناسایی آسان خطاها و مشکلات.
Seiketsu (استانداردسازی): بهکارگیری مجموعه رویکردهایی برای استانداردسازی مراحلِ Seiri، seiton و Seiso بهمنظور جلوگیری از سردرگمی کارگران.
Shitsuke (پایدارسازی): معرفی، شناساندن و آموزش شیوههای ۵S به تمام افراد بهمنظور اطمینان از اجرای درست 5S و بهبود مستمر.
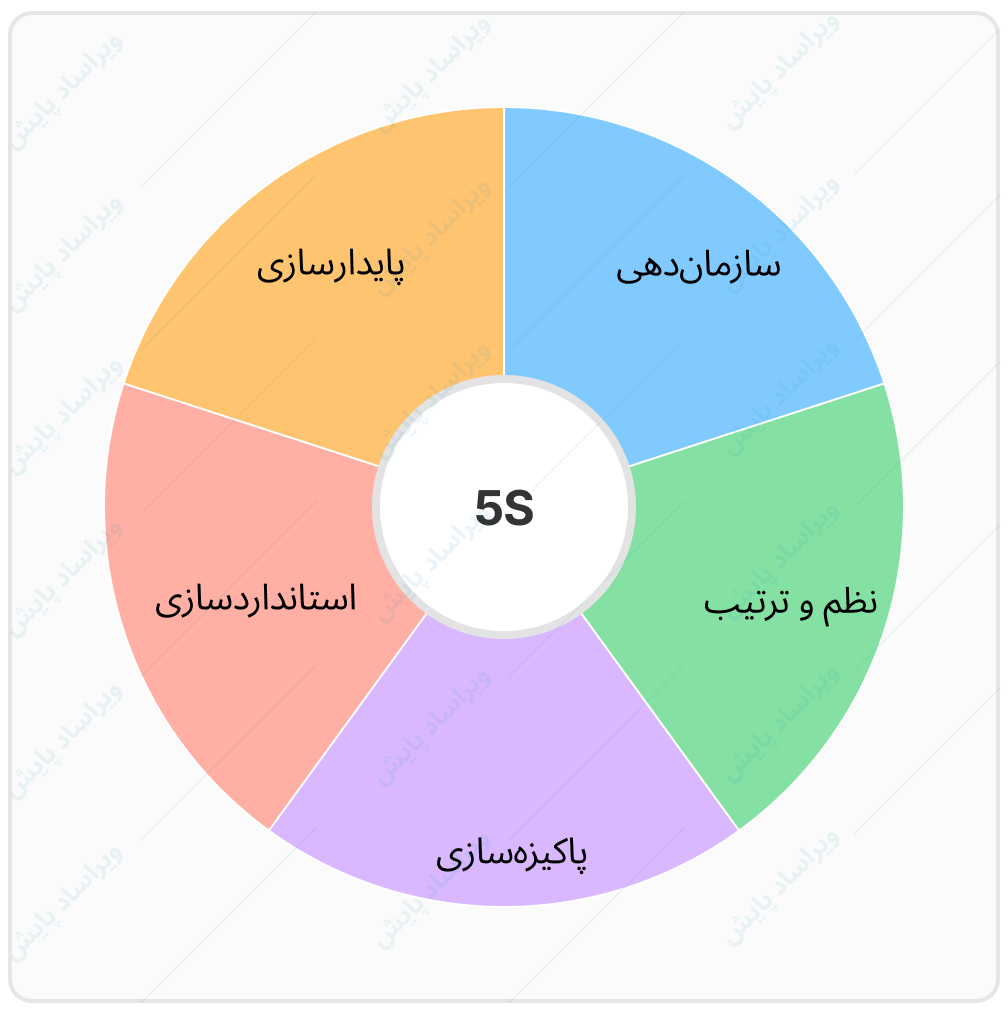
کایزن
کایزن رویکردی است که هدف آن بهبود مداوم فرایندها و عملکرد کارکنان در یک سازمان تولیدی است، همکاری مداوم کارکنان در این روش سبب ایجاد بهبودهای منظم و تدریجی میشود. نکتهٔ قابلتوجه این است که مدیران میتوانند از تکنیک کایزن بهمنظور شناسایی پیوسته مشکلات در تمام صنایع استفاده کنند و راهحلهایی برای به حداکثر رساندن رضایت مشتری و حذف ضایعات ارائه دهند، از سویی دیگر این امر منجر به استانداردسازی فرایندها و بهبود بهرهوری میشود.
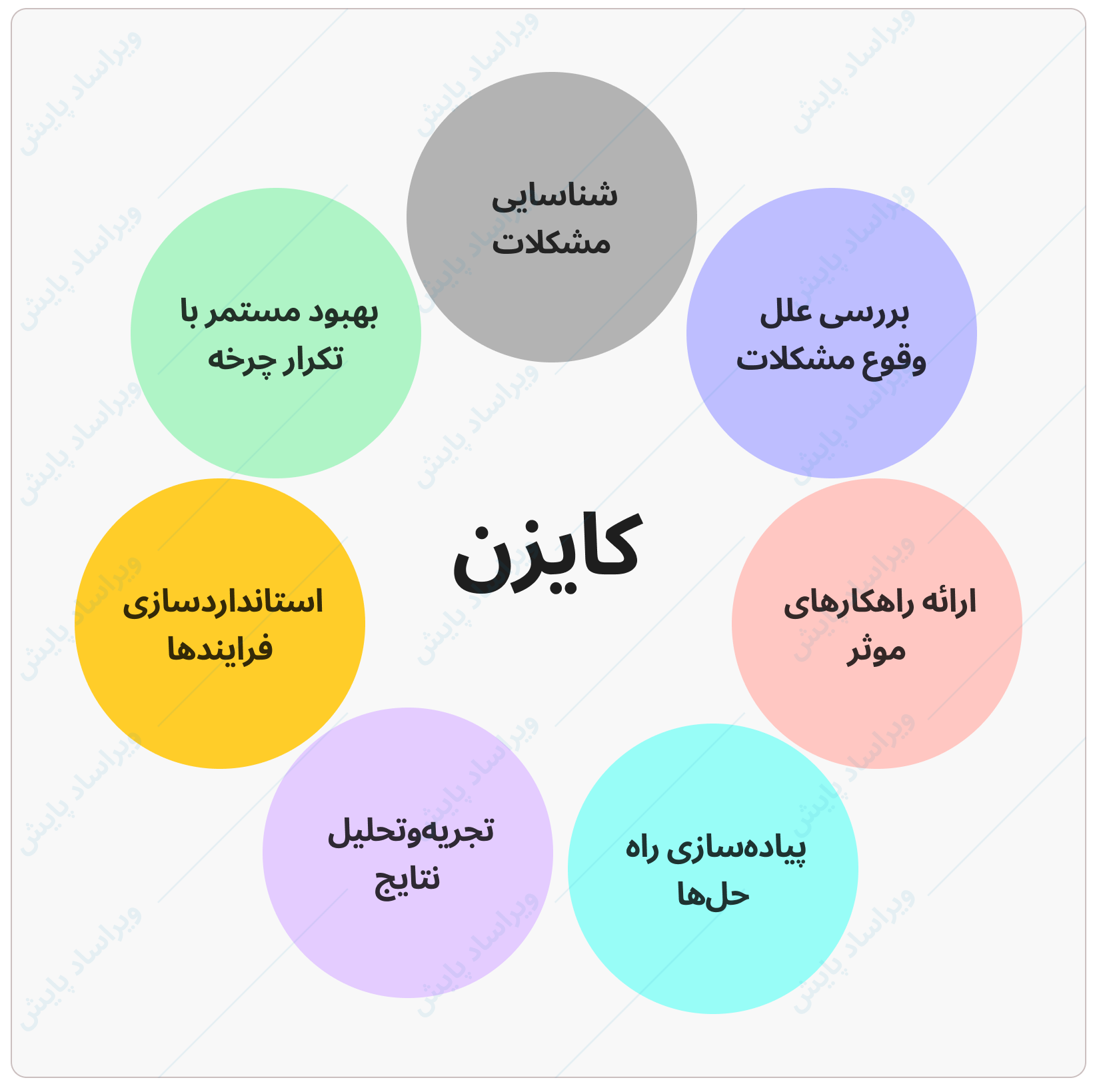
نگاشت جریان ارزش (VSM)
VSM یا همان نگاشت جریان ارزش، ابزاری است که برای ترسیم بصری جریان تولید استفاده میشود. این ابزار با ترسیم جریان تولید، وضعیت کالاها را در هر یک از مراحل نشان میدهد. VSM با کشف فرصتهای پیشرو، تولیدکنندگان را در شناسایی علل اصلی تولید ضایعات یاری میکند. از سویی دیگر VSM به کسبوکارها کمک میکند تا با تشخیص و حذف فرایندهای ناکارآمد منجر به کاهش زمان تولید و افزایش کارایی شوند.
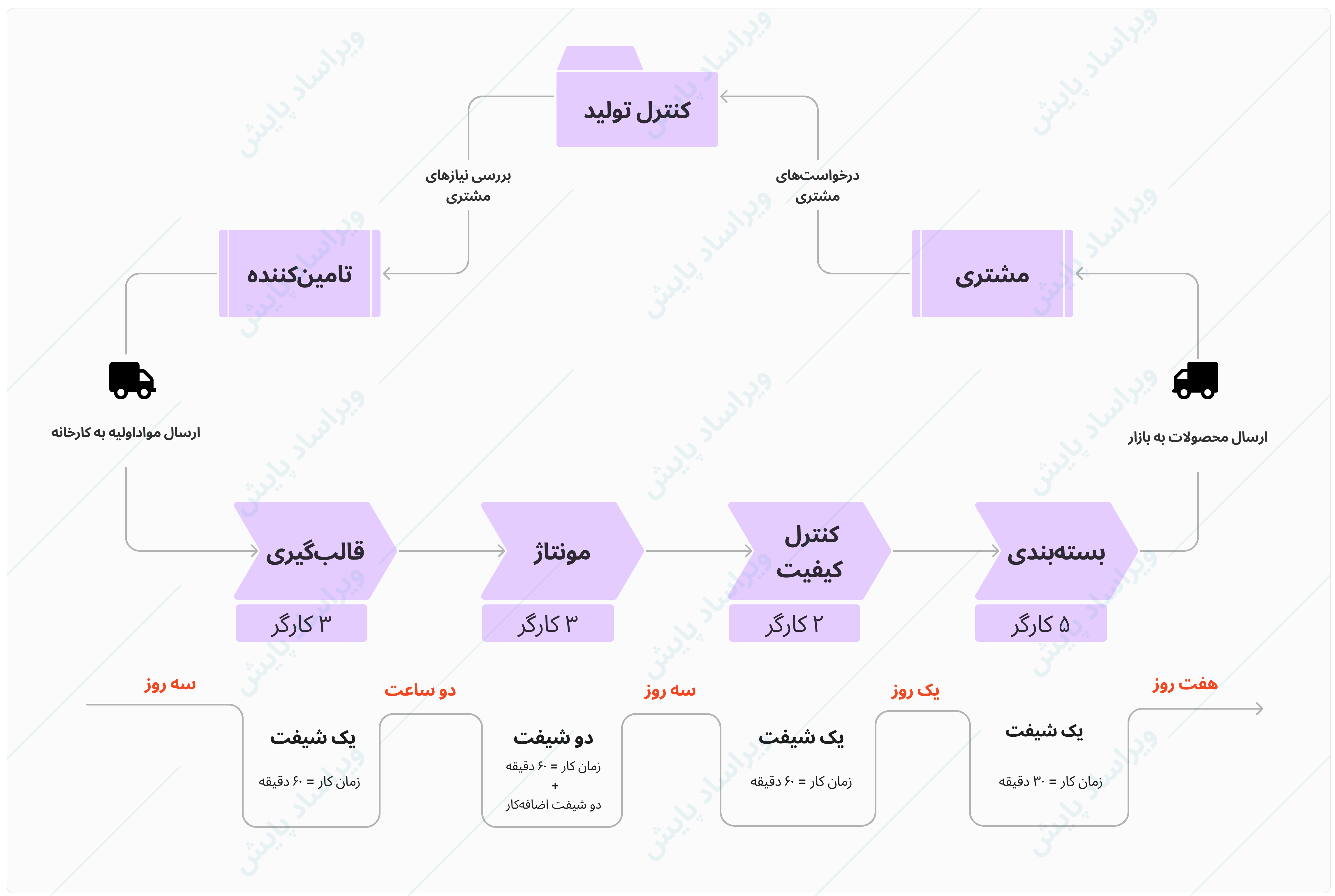
PDCA
چرخه دمینگ یا PDCA مخفف کلمات Plan - Do -Check- Act است، هدف از آن اجرای بهبود مستمر برای کنترل کیفیت فرایندها و محصولات میباشد که در نهایت منجر به کاهش هزینهها و افزایش بهرهوری میشود. این چرخه از چهار مرحله تشکیل شده است:
برنامهریزی (Plan): بررسی فرایندها و شناسایی فرصتهای پیشرو برای تغییر در برنامهریزی.
اجرا (Do): انجام تغییرات در نظر گرفته شده در مقیاسی کوچک و کنترل شده.
بررسی (Check): تجزیهوتحلیل نتایج از طریق بررسی محصولات و نظرات مشتریان.
عمل (Act): شناسایی و رفع خطاهای قبلی و ثبت تغییرات جدید بهمنظور کسب نتایج بهتر.
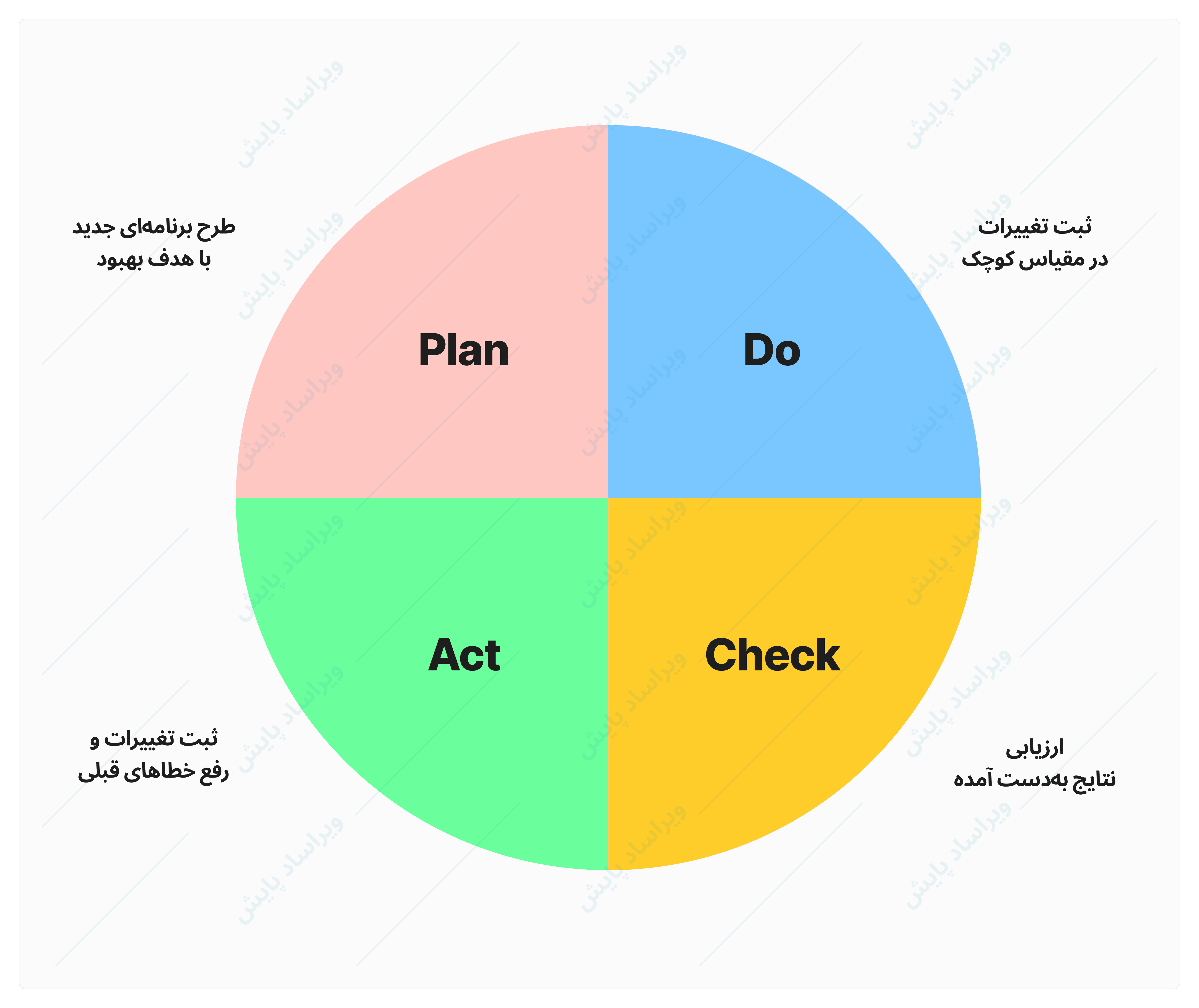
پوکایوکه
پوکایوکه (Poka-Yoke) ابزاری پیشگیرانه است که باهدف تصحیح و حذف اشتباهات مانع از ایجاد خطاها از سوی نیروی انسانی میشود و همچنین نرخ دوبارهکاری را به حداقل میرساند. از تکنیک پوکایوکه میتوان بهمنظور بررسی عیوب، جلوگیری از تولید محصولات ناقص، کاهش انحرافات تولید و اصلاح محصولات نیمهساخته استفاده کرد.
Andon
سیستم Andon سیستم هشداری است که به اپراتورها کمک میکند تا متوجه شوند چه مشکلی در خط تولید رخ میدهد؛ بنابراین آنها میتوانند به تمام افراد حاضر در کارخانه هشدار دهند که مشکلاتی مانند کمبود مواد اولیه، خرابی ماشینآلات یا مشکلات کیفی به وجود آمده است. از اینرو کسبوکارها میتوانند با استفاده از سیستم Andon مشکلات تولید را در مراحل ابتدایی تشخیص دهند و از هزینههای تولید بکاهند، این امر منجر به بهبود مستمر کیفیت و در نتیجه برآوردهشدن هر چه سریعتر نیازهای مشتریان میشود.
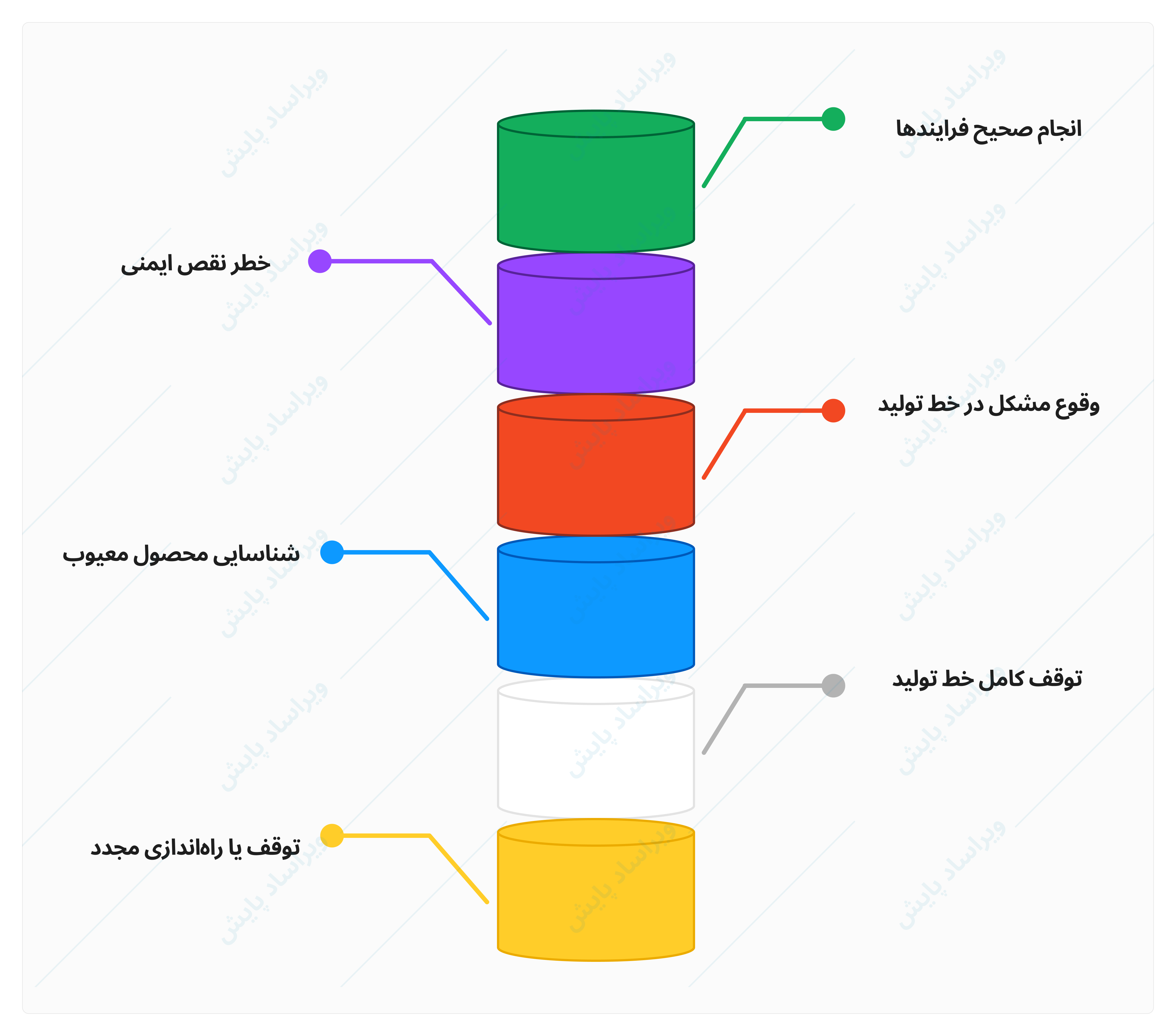
جیدوکا
Jidoka تکنیکی کاربردی برای تولید ناب است که به طور گسترده در تولید و توسعه محصولات مورداستفاده قرار میگیرد. از این تکنیک بهعنوان راهکاری ساده برای ممانعت از تولید محصولات نامرغوب استفاده میشود. هدف از بهکارگیری Jidoka توانمندسازی اپراتورها برای کنترل و نظارت همزمان چند دستگاه در خط تولید است؛ این امر به آنها کمک میکند تا بسیاری از مسائل مربوط به کیفیت را بلافاصله پس از وقوع شناسایی کنند و نرخ بهرهوری را افزایش دهند.
جیدوکا بر چهار اصل استوار است، این اصول عبارتاند از:
۱. کشف ناهنجاری
۲. توقف روند تولید
۳. برطرفکردن فوری مشکل
۴. بررسی و حل علت اصلی وقوع آن
استفاده از ابزارهای تولید ناب به کمک مانیتیت
نرمافزار هوشمند مانیتیت با ایجاد بستری بهمنظور جمعآوری یکنواخت دادهها از سراسر خط تولید، در تلاش است تا مدیران را در شناسایی زودهنگام گلوگاهها و نقاط ضررده یاری کند. این نرمافزار با بهرهگیری از مؤثرترین ابزارهای تولید ناب و ارائه دادههای بصری مانع از بیکار ماندن نیروی انسانی و تجهیزات میشود و در نتیجه افزایش بهرهوری را به همراه میآورد؛ بنابراین تولیدکنندگان میتوانند با اجرای نرمافزار مدیریت تولید مانیتیت علاوه بر نظارت ۲۴ ساعته بر خط تولید، گام بزرگی در راستای کاهش هزینهها بردارند.