منظور از تولید ناب (Lean manufacturing) استفاده از مجموعه روشهایی است که برای بهحداقلرساندن اتلاف مواداولیه و استعدادهای نیروی کار و در عین حال حفظ یا افزایش سطح تولید طراحی شدهاند و در نهایت منجر به بهبود خالص در بهرهوری کل میشوند. تولید ناب به زبان ساده بر کاهش ضایعات و ناکارآمدیها، ساخت محصولات باکیفیت و بهبود مستمر فرایند تولید تمرکز دارد.
انواع اتلاف در صنعت تولید
در تولید ناب، هر عمل یا فرایندی که مشتری مایل است در مقابل آن هزینه بپردازد ارزش نامیده میشود. از سویی دیگر هر چیزی که ارزشی به محصول اضافه نمیکند و یا منجر به سودآوری نمیشود را ضایعات مینامند، از این رو حذف ضایعات از فرایند تولید امری مهم و غیرقابلچشمپوشی است. در ادامه با 8 فرایندی که منجر به تولید ضایعات و ناکارآمدیها میشود، آشنا میشویم:
عیوب
تولید محصولات معیوب و بیکیفیت، تعمیر ضعیف ماشینآلات، بیدقتی در محاسبه موجودی، و حتی ثبت نکردن دادهها بهصورت مستمر همگی از عوامل ایجاد نقص هستند. وجود این موارد علاوه بر تولید ضایعات، هزینهها را نیز افزایش میدهد از این رو مدیران و اپراتورها میتوانند عیوب را به کمک سیستم هوشمند کنترل کیفیت شناسایی و برطرف کنند.
تولید بیش از حد
تولید بیش از حد محصول و یا سریعتر از آنچه در مراحل بعدی لازم است، منجر به ایجاد ضایعات، اتلاف زمان و مواداولیه میشود. تولید ناب با تمرکز بر تولیدِ بهموقع (JIT) تنها شامل ویژگیهای مورد پسند مشتریان است.
انتظار (کارگران بیکار یا تجهیزات بیکار)
این نوع ضایعات تنها زمانی رخ میدهد که کارکنان نمیتوانند کار کنند. از جمله هنگام طولانیشدن بیش از حد فرایند، از دسترس خارجشدن تجهیزات به دلایل متفاوت و یا حتی زمانی که تجهیزات و نیروی انسانی بهعلت فقدان موجودی کافی و مواداولیه متوقف میشوند. در این شرایط کارگران منتظر مواداولیه یا راهاندازی مجدد تجهیزات هستند، گاهی نیز ممکن است تجهیزات بیکار در انتظار تعمیر و نگهداری باشد.
پردازش بیش از حد
پردازش بیش از حد زمانی اتفاق میافتد که فرایندها خیلی آهسته پیش میروند و بهعنوان مانعی برای پیشرفت تلقی میشوند؛ برای مثال میتوان به ثبت دادههای تکراری، کُند بودن فرایندهای تأیید و گزارشدهیهای مکرر و اضافی اشاره کرد.
موجودی مازاد
وجود موجودی مازاد میتواند منجر به مشکلات متعددی از جمله عدم شناسایی بهموقع محصولات معیوب به دلیل زمان انبارش طولانی، شکلگیری ارتباط ضعیف بین تولید و تقاضا و همچنین منقضی شدن مواد اولیه در صنایعی همچون صنایع غذایی و دارویی میشود.
استعدادهای استفاده نشده
ضایعاتی که پیش از این گفته شد به طور مستقیم با فرایندهای تولید مرتبط هستند درحالیکه نادیدهگرفتن استعدادهای نیروی انسانی ناشی از ضعف در مدیریت و یا برقراری ارتباطات ضعیف و همچنین عدم مشارکت کارکنان در تصمیمگیریهاست.
هماکنون بخوانید: هوشمصنوعی چگونه میتواند باعث شکوفایی استعدادهای نیروی انسانی شود؟
حملونقل غیرضروری
جابهجایی غیرضروری کارکنان، قطعات، محصولات یا تجهیزات و ماشینآلات ناشی از برنامهریزی ضعیف تولید است که علاوه بر اتلاف زمان باعث طولانیشدن فرایند تولید نیز میشود. از اینرو تولیدکنندگان میتوانند با بهینهسازی چیدمان کارخانه و بهکارگیری نرمافزار مدیریت تولید مانع از ایجاد آنها شوند.
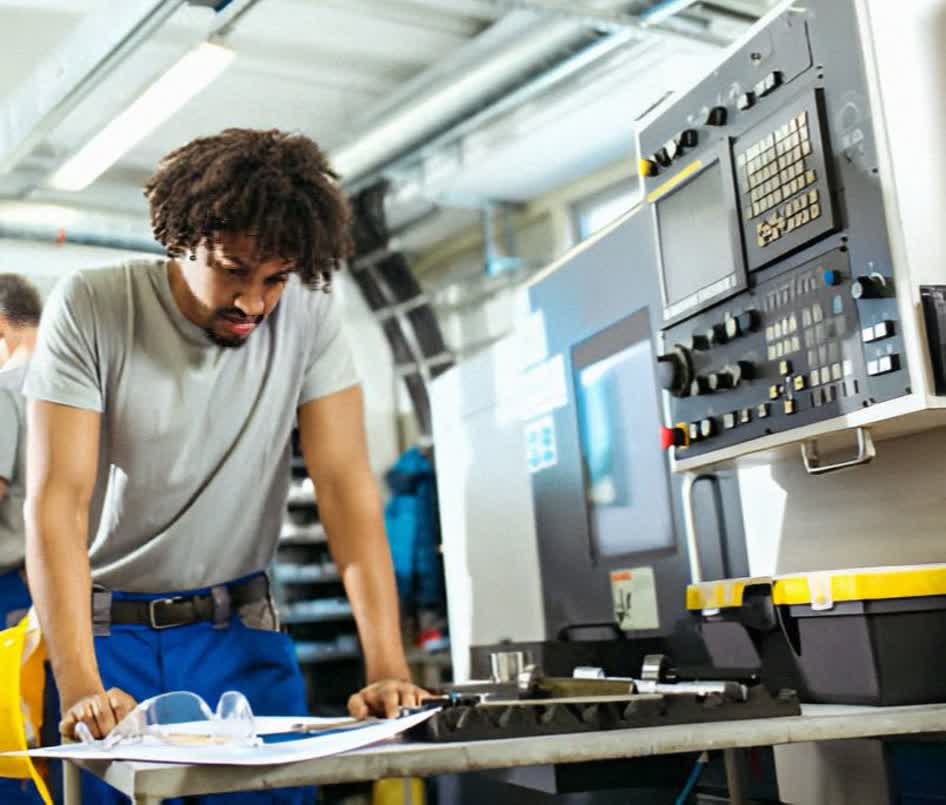
اهمیت تولید ناب در ایران
تولید ناب به انگلیسی Lean manufacturing از اهمیت بسیاری در مهندسی صنایع و کاهش حداکثری ضایعات برخوردار است. از آنجاییکه مدیران همواره به دنبال شناسایی مشکلات و بهحداقلرساندن ضایعات تولید هستند میتوانند با استفاده از روشهای تولید ناب، آموزش به کارگران، جمعآوری و بررسی دادهها و همچنین رعایت اصول تولید ناب مانع از ایجاد ضایعات بیشتر و هدررفت بخش عظیمی از سرمایه شوند.
مزایای تولید ناب در مهندسی صنایع
در ادامه به برخی از مزایای استفاده از تکنیکهای تولید ناب میپردازیم:
بهبود کیفیت
بهبود فرایندها به طور طبیعی منجر به تولید محصولات باکیفیت میشود. از این رو تولیدکنندگان میتوانند با رعایت اصول تولید ناب و بهکارگیری ابزارهای آن کیفیت مواد اولیه ورودی و محصولات تولید شده را تضمین کنند. FabriQC و PartQC ابزارهایی هستند که اپراتورها میتوانند به کمک آن دو عیوب را در حین تولید شناسایی و به دنبال آن مشکلات موجود را برطرف سازند.
مدیریت موجودی
سیستم ناب به مدیران کمک میکند تا با مدیریت موجودی کارخانه و تولید بهموقع مانع از ایجاد مشکلات جدید و ساخت محصولات نیمهساخته شوند و به دنبال آن بسیاری از هزینهها را کاهش دهند.
کاهش زمان تولید
اتلاف وقت و طولانیشدن چرخه تولید به معنای هدررفت سرمایه است. این امر تولیدکنندگان را به سمت یافتن راهکارهایی برای کاهش زمان تولید و کوتاهشدن چرخه تولید سوق میدهد. بهکارگیری روشهای تولید ناب منجر به صرفهجویی در زمان تولید، کاهش هزینهها و ارائه محصولات در کوتاهترین زمان ممکن خواهد شد.
کاهش ضایعات
به طور کلی، هر ماده یا محصول تولید شده در حین فرایند تولید که بخشی از محصول نهایی نیست را ضایعات تولید مینامند. جالب است بدانید که تولید ضایعات از بزرگترین مشکلات موجود در هر کسبوکاری محسوب میشوند. کاهش ضایعات کارخانه منجر به تولید محصولات باکیفیت، افزایش بهرهوری و کاهش هزینهها میشود، به همین دلیل سازمانها با رویآوردن به مفاهیم تولید ناب از ایجاد بخش انبوهی از ضایعات جلوگیری کنند.
اصول تولید ناب چیست؟
رعایت 5 اصل تولید ناب به مدیران کمک میکند تا با حذف هرچه بیشتر ضایعات، بهبود فرایندهای تولید را رقم بزنند. در ادامه با پنج اصل مدیریت تولید ناب که برای بهینهسازی سیستمهای ناب به کار میروند و فضای هر کسبوکاری را سازمان یافتهتر و کارآمدتر میکند، آشنا میشویم:
شناسایی ویژگیهای مورد پسند مشتریان (Specifying value)
در دنیای ناب، ارزش چیزی است که مشتری حاضر است در ازای آن هزینه بپردازد. بنابراین تمام فرایندهای تولید باید در جهت برآوردهکردن نیازهای مشتریان انجام شود. پس اولین گام در فرایند تولید ناب، شناسایی ویژگیهای مهم و غیرمهم محصولات از نظر مشتریان است. مدیران میتوانند با تشخیص ویژگیهای حائز اهمیت، تنها محصولاتی با این ویژگیها را تولید کنند؛ زیرا مشتریان تنها در ازای دریافت محصولی با ویژگیهای مطلوب حاضر به پرداخت هزینه میشوند.
ترسیم جریان ارزش (Map the value stream)
این اصل شامل تجزیهوتحلیل مواداولیه و منابع موردنیاز برای تولید محصولات است و بهمنظور افزایش بهرهوری و ارائه خدمات بهتر به مشتریان انجام میشود. به عبارتی دیگر؛ حاوی مجموعه اقدامات یا مراحلی است که به مدیران اجازه میدهد تا با بررسی تمام فرایندهای تولید، فرصتهای پیشرو و منابع تولید ضایعات را شناسایی کنند.
ایجاد جریان ارزش (Flow the value)
یکی از اهداف تولید ناب، بهبود فرایند است. فرایند تولید را میتوان با تشخیص ضایعات یا ناکارآمدیها، ایجاد برنامهای یکپارچه برای تولید و رفع موانع عملکردی بهینه ساخت و مانع از ایجاد گلوگاهها و توقفات شد.
سیستم کشش (Pull system)
تولید محصولات در سیستم کششی تنها بر اساس نرخ تقاضا انجام میشود. بهعبارتی دیگر؛ هرچه تقاضا بیشتر باشد، تولید محصولات افزایش مییابد. این رویکرد با حذف مراحل غیرضروری از جمله حملونقل مواد، تولید بیش از حد محصولات و ذخیره موجودی مازاد به تولیدکنندگان در مدیریت ضایعات یاری میرساند.
بهبود مستمر یا کایزن ontinuous improvement
انجام چهار مرحله اول از اصول تولید ناب، بسیار مهم است؛ اما رعایت اصل پنجم از مهمترین مواردی است که باید به آن توجه کرد. این اصل بر بهبود مستمر فرایندها باتکیهبر ابزارهای تولید ناب و روشهای آن اشاره دارد.
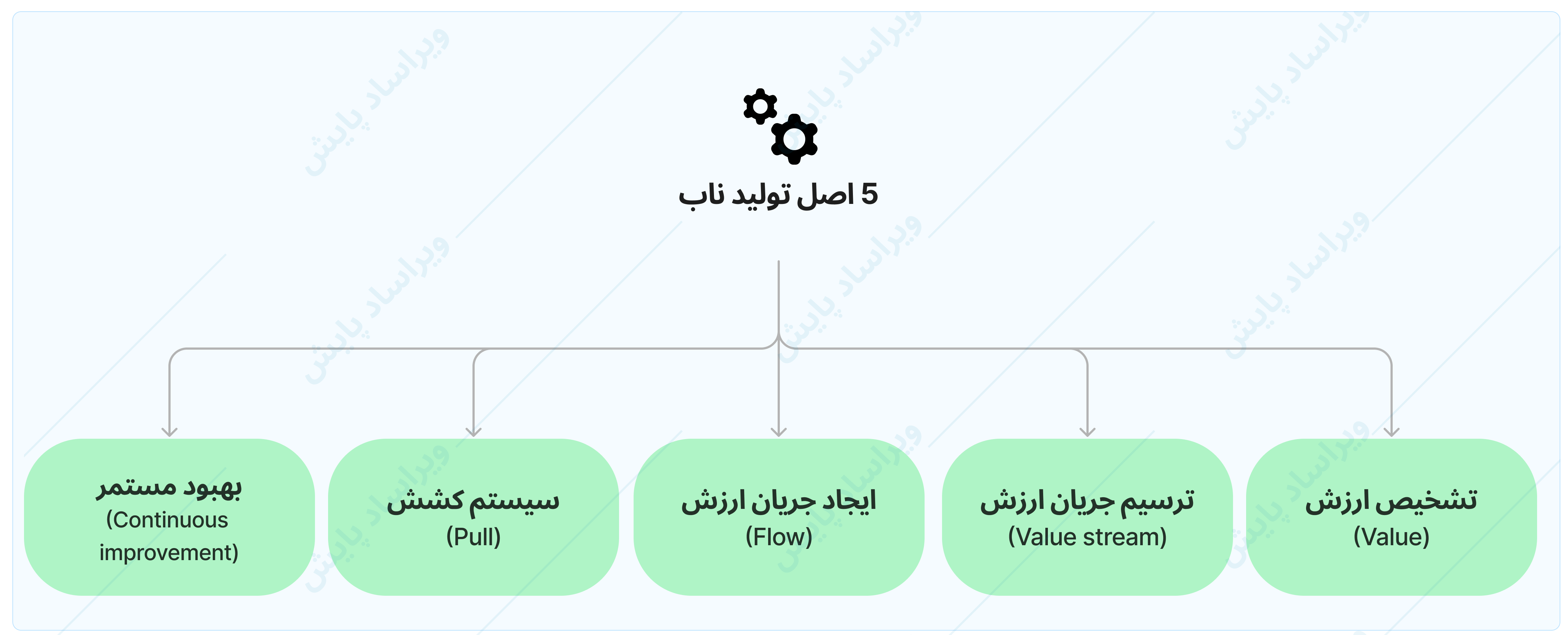
ابزارها و تکنیکهای تولید ناب
فلسفه تولید ناب تنها بهمنزلهٔ پیروی از قوانین و استانداردها نیست بلکه نیازمند تغییر ذهنیت کارکنان مجموعه و حرکت بهسوی یادگیری، نوآوری و چابکی است. به عبارتی دیگر؛ هدف از تولید ناب بهکارگیری مجموعهای از ابزارها و تکنیکهایی بهمنظور ایجاد ارزش بیشتر برای مشتریان و کاهش ضایعات در فرایند تولید است. برخی از این ابزارها عبارتاند از:
5S
سیستم 5S یا نظام آراستگی یکی از ابزارهای مدیریت ناب و روشی برای سازماندهی امکانات کسبوکارها بهمنظور اطمینان از کاهش حداکثری ضایعات و افزایش بهرهوری است. 5S از پنج اصطلاح ژاپنی و مرتبط به هم تشکیل میشود که عبارتاند از:
Seiri (ساماندهی): حذف اقلام و وسایل غیرضروری در فرایند تولید و مرتبسازی وسایل و ابزارهای موردنیاز.
Seiton (نظم و ترتیب): طبقهبندی و قراردادن اقلام ضروری در جای مناسب بهمنظور کاهش جابهجایی کارگران.
Seiso (پاکیزهسازی): پاکیزه نگهداشتن ماشینآلات و محیط کار بهمنظور جلوگیری و ازبینبردن مشکلاتی که ناشی از عدم پاکیزگی است.
Seiketsu (استانداردسازی): بهکارگیری روشهایی بهمنظور استانداردسازی مراحل، ساماندهی، نظم و ترتیب و پاکیزهسازی.
Shitsuke (پایدارسازی): معرفی، شناساندن و آموزش ۵S به تمام افراد کارخانه بهمنظور اطمینان از اجرای درست 5S و تداوم پیشرفت.
پوکایوکه
پوکایوکه (Poka-Yoke) ابزاری است که با تصحیح و حذف اشتباهات مانع از ایجاد خطا از سوی نیروی انسانی میشود. برای مثال در تجهیزاتی که با فشردن دکمه فعال میشوند، از اپراتور میخواهند تا قبل از فشردن دکمه کلیدی را بچرخاند. این امر به اپراتور کمک میکند تا از فعالسازی ناآگاهانه تجهیزات جلوگیری کنند.
کانبان
کانبان (Kanban) روشی برای مدیریت تولید ناب در کارخانهها است که بهمنظور تجسم گردشکار استفاده میشود. این سیستم با اولویتبندی و تقسیم وظایف به مدیران اجازه میدهند تا پیشرفتها را پیگیری کنند و مانع از بیکاری کارگران شوند.
کایزن
کایزن رویکردی است که بر بهبود مستمر تأکید دارد و به کسبوکارها اجازه میدهد تا به طور دائم مشکلات را شناسایی کرده و راهحلهایی برای به حداکثر رساندن رضایت مشتری و حذف ضایعات ارائه کنند. کایزن شامل ایجاد تغییرات کوچک و تدریجی در طول فرایند تولید است که باعث بهبود عملکرد تمامی افراد و ماشینآلات میشود.
آندن (Andon)
Andon سیستم هشداری است که در تأسیسات تولیدی پیادهسازی میشود. اپراتورها میتوانند به کمک آندن به تمام افراد کارخانه هشدار دهند که مشکلاتی مانند کمبود مواد اولیه، خرابی ماشینآلات یا مشکلات کیفی بهوجود آمده است. واچرجت (WatcherJet) ابزاری سودمند و مجهز به سیستم هشدار است که همچنین قادر به جمعآوری خودکار دادههای خط تولید میباشد.
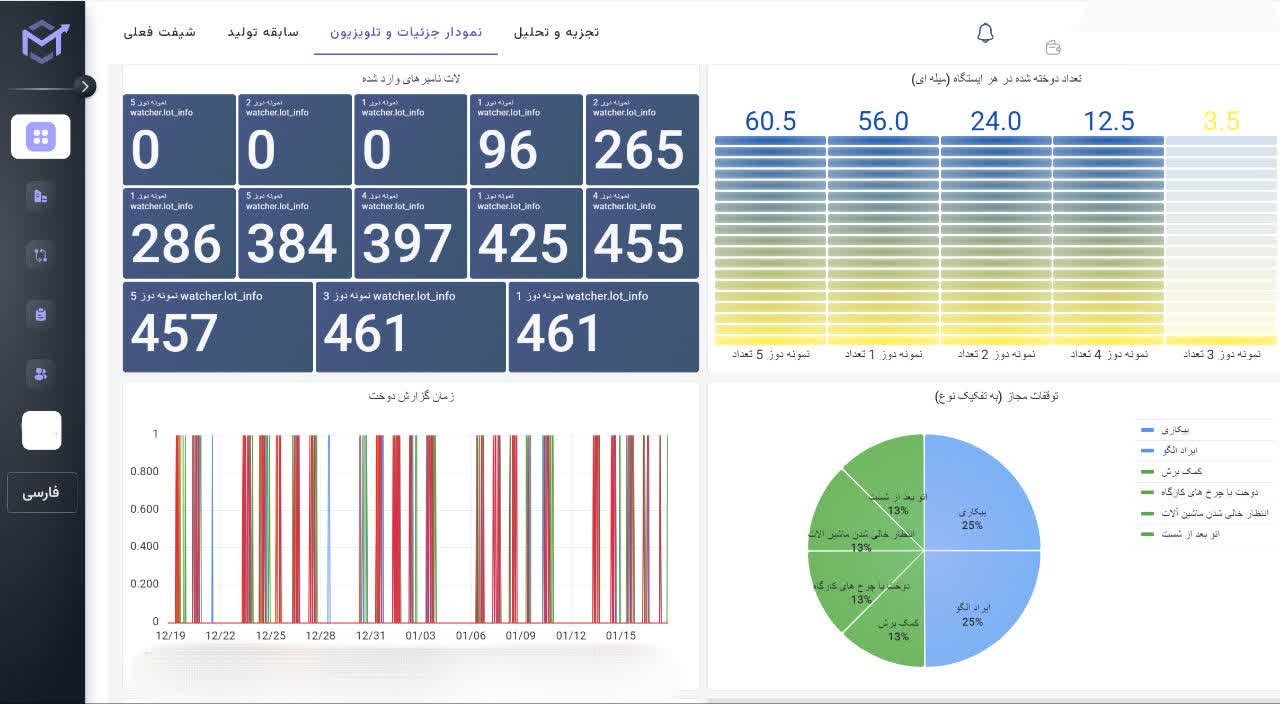
مراحل پیادهسازی تولید ناب در صنایع
۱. شناسایی و کاهش ضایعات تولید
یکی از مهمترین و پرچالشترین مشکلات هر کارخانهای تولید ضایعات در حجم انبوه است. به همین دلیل مدیران همواره به دنبال تعیین منابع ضایعات و کاهش حداقلی آنها هستند. یکی از راههای شناسایی منابع تولید ضایعات، جمعآوری دقیق و مستمر دادههای تولید است. مدیران میتوانند پس از تحلیل دادهها عملکرد خط تولید را از طریق ردیابی OEE ارزیابی و نظارت کنند و از تولید حجم بسیاری از ضایعات ممانعت به عمل بیاورند.
۲. دیجیتالسازی کارخانه
سیستم مانیتورینگ با قابلیت نمایش آنلاین رخدادهای تولید بینشی جامع و روشن از عملکرد خط تولید را در اختیار تولیدکنندگان میگذارد. همچنین مدیران با وجود این سیستم میتوانند گلوگاهها و مشکلات موجود را شناسایی کنند و اقدامات لازم جهت برطرفسازی آنها را انجام دهند. نرمافزار مانیتورینگ با قابلیت پردازش و تجزیهوتحلیل دادههای جمعآوری شده مدیران را قادر میسازد تا ابزارهای مؤثری برای نظارت آنی بر روند کیفیت و عملکرد خط تولید را به کار گیرند.
۳. توانمندسازی و تعامل اپراتورها
وجود نیروی انسانی ماهر و توانمند نقش بسزایی در تولید ناب و کاهش ضایعات دارد. حال اگر داشبوردی بصری در اختیار اپراتورها قرار گیرد تا آنها بتوانند بهراحتی عملکرد کارخانه را مشاهده و ردیابی کنند، تعامل اپراتورها با فرایند تولید افزایش مییابد و بیشازپیش از مشکلات تولید آگاه میشوند.
پیادهسازی تولید ناب به کمک نرمافزار مانیتیت
همانطور که پیشتر اشاره کردیم، تولید ناب شامل مجموعهٔ گستردهای از ابزارها و مفاهیمی است که همگی آنها فرایند تولید را به سمت کارآمدی و افزایش بهرهوری هدایت میکند. تولیدکنندگان بهمنظور بهرهمندی از مزایای سیستم ناب نیازمند یادگیری مستمر و پیادهسازی مؤثر و همچنین نرمافزار تولید ناب هستند.
نرمافزار هوشمند مانیتیت باتکیهبر هوش مصنوعی بهعنوان بستری بهمنظور جمعآوری و تحلیل دادهها نقش بسزایی در سیستم ناب ایفا میکند. این نرمافزار هوشمند با قابلیت ردیابی OEE و نظارت بر دادههای تولید منجر به شناسایی سریعتر منابع ایجاد ضایعات و کاهش حداکثری آنها میشود. از اینرو سازمانها میتوانند با در اختیار داشتن داشبورد اختصاصی، به صورت آنلاین و لحظهای بر فرایند تولید نظارت کنند.