اندازه گیری شاخص OEE بهترین روش برای شناسایی نقط ضعف است. تولیدکنندگان با محاسبه OEE، بینش مهمی در مورد چگونگی بهبود سیستماتیک فرایند تولید بهدست میآورند. از سویی دیگر OEE بهترین KPI برای شناسایی گلوگاهها، معیار پیشرفت و همچنین بهبود بهرهوری تجهیزات تولیدی (یعنی کاهش ضایعات) است که نه تنها توانایی تشخیص موقعیت تولید را دارد، بلکه میتواند فرایندهای تولید را به سمت بهبود سوق دهد.
همانطور که میدانید؛ فرآیند تولید از تعامل نیروی انسانی، ماشینآلات و مواداولیه تشکیل میشود و محصول نهایی را به مشتری ارائه میدهد. این فرایند با فاکتورهای کیفیت، هزینه و تحویل بهموقع سنجیده میشود تا به کمک آن سودآوری و ماندگاری فرآیندها را محقق و تضمین نماید. محاسبه اثربخشی کلی تجهیزات میتواند هرگونه خسارت و ضرر و زیان را بلافاصله نشان دهد. از طرف دیگر تمام پرسنل نیز میتوانند عملکرد کلی را بررسی و تحلیل کنند و اقدامات لازم جهت حل مسائل را انجام دهند؛ به همین دلیل بهکارگیری روش OEE میتواند نقش بسیار مهمی در بهبود عملکرد نیروی انسانی ایفا کند.
اثربخشی کلی تجهیزات یا OEE استاندارد طلایی برای اندازهگیری بهرهوری تولید است. این یکی از مفاهیم اساسی در تولید ناب و محرک عملکرد کلیدی برای هر کارخانه تولیدی، واحد تولیدی، کارگاه یا ایستگاه فردی است و از فرمول زیر پیروی میکند:
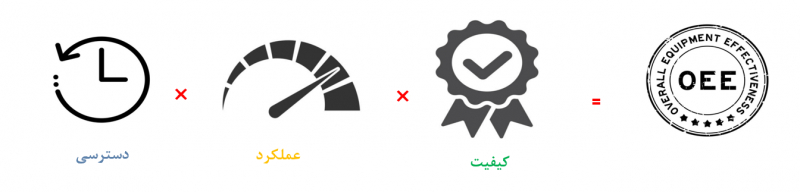
دسترسی (زمان در دسترس تولید): زمانی که یک دستگاه برای تولید در دسترس است.
عملکرد: تعداد قطعاتی که با سرعت متوسط در یک بازه زمانی تولید میشود.
کیفیت: تعداد محصولاتی که بینقص تولید شده اند.
به عنوان مثال؛ ماشینی که ۹۰ درصد مواقع در دسترس است، امتیاز ۹۵ درصد از عملکرد را دارد و ۹۸ درصد از مواقع محصولات با کیفیتی تولید میکند، و در نتیجه ۸۳.۷۹ درصد OEE خواهد داشت.
خطاهای رایج در محاسبه و ارزیابی OEE
دسترسی
تلفات ناشی از عدم دسترسی تجهیزات و ماشینآلات متنوعترین و رایجترین علت ایجاد مشکلات در هنگام محاسبه و تحلیل OEE است. برای مثال یکی از اشتباهات رایج در هنگام محاسبه شاخص اثربخشی کلی، تمایل مدیران به حذف زمان توقفات ناشی از اعمال تغییرات در خط تولید و یا زمان استراحت و نهار کارگران است.
عملکرد
یکی دیگر از مشکلات گسترده این است که سازندگان حداکثر توان بالقوه ماشینآلات خود را نمیدانند و در بیشتر موارد سرعت واقعی تولید را نادیده میگیرند. درنتیجه عملکرد بیش از ۱۰۰% محاسبه میشود؛ بنابراین مقدار OEE بهدستآمده نادرست است.
کیفیت
مشکلات ناشی از کیفیت اغلب به علت شمارش دستی محصولات معیوب توسط نیروی انسانی و یا جمعآوری دیرهنگام دادههای حاصل از تولید رخ میدهد؛ از اینرو بهترین روش استفاده از نرمافزار مدیریت تولید با قابلیت جمعآوری خودکار دادهها و همچنین شناسایی آنی خطاها و محصولات ناقص و بیکیفیت است.
هوش مصنوعی چگونه میتواند یاریگر نیروی انسانی در فرایندهای تولید باشد؟
اهمیت ارزیابی فرایندهای صنعتی به کمک OEE
مقادیر بهدستآمده از محاسبه OEE، بینش روشن و ارزشمندی از فرایندهای تولید، ردیابی پیشرفتها و نحوه عملکرد کارگران و ماشینآلات را در اختیار تولیدکنندگان میگذارد. گرچه ممکن است این فرایند کمی زمانبر به نظر برسد؛ اما با محاسبه شاخص OEE و ارزیابی فرایندهای صنعتی بسیاری از دلایل کاهش بهرهوری مشخص خواهد شد. برای مثال؛ مدیران با محاسبه OEE متوجه میشوند که ماشینآلات همیشه منبع ناکارآمدی نیستند و گاهی اوقات کارکنان با انجام خطا منجر به کاهش بهرهوری میشوند.

چرا باید از OEE استفاده کنیم؟
کاهش خرابی تجهیزات
خرابی تجهیزات و توقفهای برنامهریزی نشده موجب کاهش بهرهوری میشوند. برای به حداقل رساندن توقفات، انجام منظم فرایند تعمیر و نگهداری، بررسی مدت زمان توقف دستگاه، بررسی دلایل خاموشی تجهیزات و همچنین بررسی علل خسارات امری ضروری است. از سویی دیگر تکرار توقفات جزئی موجب افزایش خسارت و اتلاف وقت میشود و در روند تولید اثر میگذارد. اطلاع رسانی و اقدام سریع، بررسی الگوهای کاهش عملکرد (مانند بررسی زمانهایی که توقفهای جزئی اتفاق می افتد) و همچنین نظارت بر استانداردسازی فرایند و نیروی کار موجب کاهش توقفات و اتلاف وقت میشود.
کاهش زمان راهاندازی و تنظیم ماشینآلات
فرایند تنظیم تجهیزات از جمله توقفات برنامهریزی شده محسوب میشود و زمانی اتفاق میافتد که دستگاه برای ساخت محصولی متفاوت، تعویض میشود و یا زمانی که تجهیزات برای انجام تعمیرات و نگهداری پیشگیرانه خاموش میشوند. برای کاهش اتلاف وقت در این گونه موارد بهتر است محصولاتی که در یک دسته قرار دارند را در یک دوره تولید کرد تا نیازی به تعویض تجهیزات نباشد همچنین میتوان از سریعترین و ایمنترین روش برای تغییر تجهیزات و تولید محصولات متفاوت استفاده کرد.
بهینهسازی چرخه تولید
کاهش سرعت تجهیزات نیز در کاهش تولید موثر است و به عواملی مثل فرسودگی دستگاهها، تعمیر و نگهداری ضعیف، سایش قطعات، مشکلات برقی و عدم مدیریت صحیح مربوط میشود. با تعمیر و نگهداری صحیح تجهیزات، بررسی و ارزیابی مستمر عملیات، میتوان چرخه تولید را بهبود بخشیده و از بروز خسارتها جلوگیری کرد.
کاهش هدر رفت ناشی از کیفیت
تولید محصولات ناقص و بیکیفیت ممکن است به دلایل مختلفی همچون نقص فرایند، کاهش عملکرد، خطای اپراتور، استفاده از مواد اولیه بیکیفیت و عدم کنترل کیفیت رخ دهد و در نهایت موجب نارضایتی مشتریان و کاهش درآمد کارخانه میشود. از اینرو تولیدکنندگان میتوانند به کمک دو ابزار کاربردی FabriQC و PartQC از انجام صحیح فرایند کنترل کیفیت اطمینان یابند. از سویی دیگر نظارت مستقیم روی تجهیزات، تعویض قطعات و تعویض دستگاههای فرسوده تأثیر مستقیمی در سطح کیفیت محصولات نهایی دارد؛ لذا لازم است نقصها را به طور مستمر پیگیری و برطرف کرد.
کاهش ضایعات
استفاده از محصولات اولیه بیکیفیت باعث هدررفتن بخش عظیمی از سرمایه و انجام دوباره فرایندها میشود. در نتیجه تولید با سرعت مطلوبی پیش نمیرود و نرخ عملکرد کاهش مییابد. این درحالی است که تولیدکنندگان میتوانند با محاسبه OEE، بر فرایند کنترل کیفیت نظارت کنند و مانع از اتلاف عملکرد و تولید محصولات ناقص شوند.
نحوه اندازهگیری بهرهوری کارخانه از طریق محاسبه OEE
مدیران و اپرتورها بهمنظور تعیین بهرهوری کارخانه، مقادیر بهدست آمده از محاسبه OEE را با توجه به سه بازه زیر اندازهگیری میکنند:
۰-۴۰
وجود شاخص کنترل تولید در این بازه به معنی نامطلوب بودن وضعیت واحد یا سازمان تولیدی است. مدیر تولید با سنجش و برطرفکردن عوامل بهوجود آمدن آن میتواند تا حد زیادی انحرافات بوجود آمده را رفع کند؛ عواملی مانند آموزش غیراصولی پرسنل، غیرواقعی بودن برنامه تولید نسبت به ظرفیت ماشینآلات، نگهداری و تعمیر چندباره ماشینآلات و تامین مواد اولیه نامطلوب سبب کاهش مقدار OEE خواهد شد.
۶۰-۴۰
این بازه بیانگر متوسط بودن وضعیت واحد تولیدی است و مدیر تولید میتواند با برطرف کردن موانع، انحرافات بهوجود آمده را کمتر کند و با بهبود OEE، بهرهوری را افزایش دهد.
۶۰-۸۰
این بازه بیانگر وضعیت مطلوب واحد تولیدی است. مدیر تولید میتواند با استمرار در جهت افزایش نرخ پارامترهای دخیل در OEE این وضعیت مطلوب حفظ کند. البته اگر نرخ بدست آمده در این شاخص عددی بالاتر از 80 باشد، وضعیت سازمان تولیدی در وضعیت خیلی مطلوب قرار میگیرد.
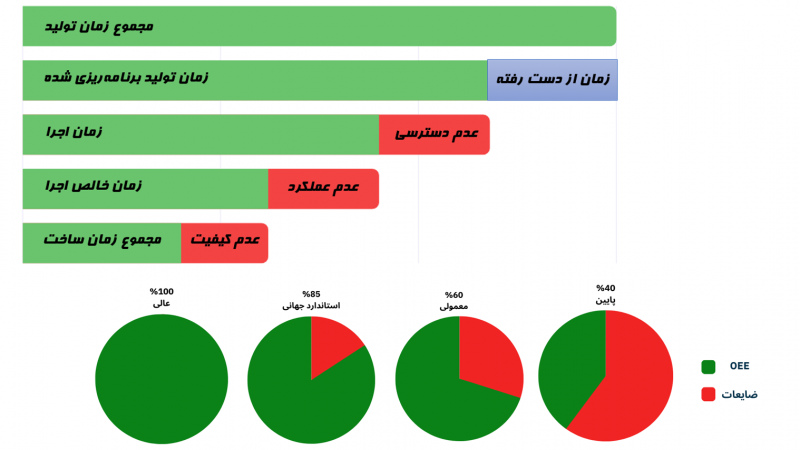
از سویی دیگر OEE پایین به معنی وجود ظرفیت پنهان یا منابع استفاده نشده در کارخانه است.
بهبود OEE در مهندسی صنایع
بهبود OEE منجر به ایجاد فرایندهای کارآمد در صنایع تولیدی و بهدنبال آن افزایش سوددهی میشود. بهترین راه برای بهبود شاخص اثربخشی کلی، کاهش میزان هدر رفت است که موجب کاهش بهرهوری در فرایند تولید میشود. تعمیر و نگهداری نادرست ماشینآلات تأثیر مستقیمی بر روی خرابی تجهیزات دارند و خسارات بسیاری را به بار میآورد، به علاوه تجهیزاتی که مدام خراب میشوند را نمیتوان در شرایط تولید حداکثری نگه داشت؛ زیرا موجب طولانیشدن زمان ایدهآل تولید و افزایش تولید محصولات ناقص میشود. این امر نشاندهنده اهمیت اجرای فرآیندهای پیشگیرانه و تعمیرات و نگهداری صحیح برای تولید بهصرفه است.
از اثرات مثبت بهبود شاخص OEE میتوان به افزایش ظرفیت تولید، بهبود کیفیت، کاهش هزینهها و افزایش اثر بخشی اشاره کرد.
از OEE در تمام صنایع تولیدی استفاده میشود و تولید فرآیندی تا تولید گسسته را در بر میگیرد؛ لذا محاسبه و اندازهگیری آن نیازمند افزودن دادههای معتبری است که از خط تولید جمعآوری میشوند. جمعآوری دادهها مهمترین مرحله از OEE به شمار میآید؛ زیرا در اختیار داشتن دادههای صحیح منجر به بدست آوردن مقدار دقیق OEE میشود. بنابراین، هرچه اعتبار دادههای بدست آمده بیشتر باشد، محاسبات با دقت بیشتری صورت میگیرد.
روشهای جمعآوری دادههای صنعتی
در مجموع از ۴ روش زیر برای جمعآوری دادههای صنعتی استفاده میشود:
افزودن دستی دادهها
در این روش، تولیدکنندگان فردی را مسئول جمعآوری دادهها قرار میدهند. این شخص مسئولیت شمارش تعداد قطعات تولید شده، شمارش تعداد قطعات معیوب، زمان توقف دستگاه و دلایل خرابی را در یک دوره زمانی برعهده میگیرد. سپس این دادهها را در یک فایل اکسل وارد کرده و محاسبات لازم را روی آن انجام میدهد و در نهایت آن را در اختیار کارکنان مربوطه میگذارد.
از جمله معایب این روش وابستگی به حضور مستقیم نیروی انسانی و احتمال وجود خطاهای بسیار است که منجر به جمعآوری دادههای غلط و ایجاد برنامه نامناسب برای تولید آینده میشود.
اسکن بارکدها یا کدهای QR
افزودن دستی اعداد و گزارشها در دراز مدت به امری ملالآور و کسالتبار تبدیل میشود و انگیزه کارکنان را از بین خواهد برد، بنابراین میتوان گفت که اسکن کدهای QR، به علت کاهش خطا تا حدی از روش قبلی کاربردیتر است. در این روش میتوان از اسکنرهای دستی و همچنین تبلت یا موبایل بهمنظور جمعآوری دادهها استفاده نمود.

واچر جتها (watcher-jet) و سایر سخت افزارهای مبتنی بر حسگر
در ایستگاههایی که تولید به صورت پیوسته انجام میشود بهتر است از سخت افزارهایی که به صورت خودکار دادهها را جمعآوری میکنند مثل watcher-jet استفاده شود. این سخت افزار، سیگنال و اطلاعات مربوط به تولید را با اتصال ایزوله الکتریکی مستقیماً از دستگاه دریافت میکند. واچرها را میتوان مستقیماً به دستگاه متصل و یا در عملگرها نصب کرد تا دادههای خود را به طور خودکار از طریق شبکه (Wi-Fi, LAN, Cellular) به نرم افزار ارسال کنند.
واچرهای پیشرفته، سایر دادههای بهدست آمده از دستگاه مثل جریان الکتریکی و دما را جمعآوری میکنند و پردازشهایی را با هدف تعمیر و نگهداری و پیشبینی حوادث انجام میدهند.
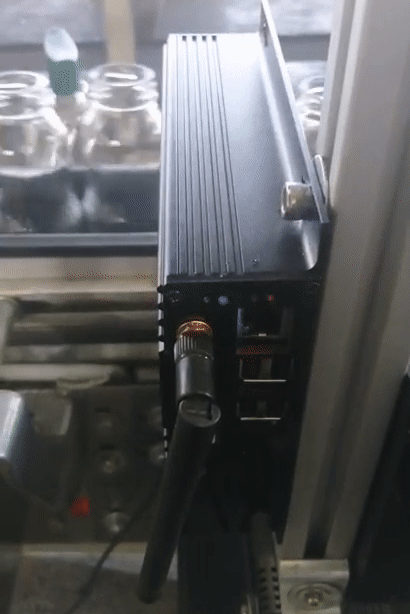
واچرکمها (Watcher-cam) و سایر دادههای ورودی دوربین
Watcher-cam بهمنظور کنترل آنلاین (زنده) فرایند تولید در فواصل دور و نزدیک و همچنین ایستگاههایی که از طریق دوربین قابل مشاهده اند استفاده میشود. این دادههای تصویری برای آگاهی از تعداد قطعات، سرعت خط تولید، کیفیت محصولات و نمای کلی ایستگاه بهکار گرفته میشود.
کنترل مستمر دادهها منجر به افزایش کارکرد تجهیزات و ماشین آلات میشود امری که جز به کمک هوش مصنوعی ممکن نخواهد بود.
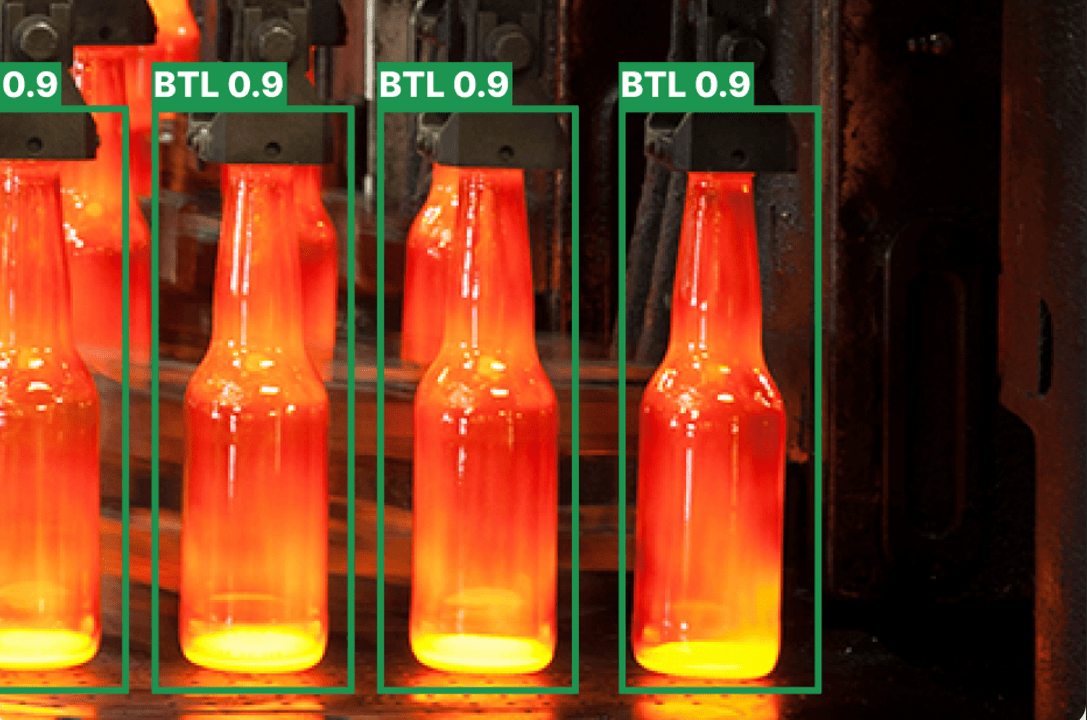
همین حالا دست به کار شوید!
با وجود اینکه جمعآوری دادهها به هر طریقی ممکن است اما استفاده از هوشمصنوعی تاثیر بسزایی در بهدستآوردن دادههای دقیق، افزایش سرعت تولید، کاهش ضایعات و تعیین برنامه معتبر تولید خواهد داشت. اکنون که درک خوبی از نحوه جمعآوری دادههای مورد نیاز برای محاسبه OEE دارید میتوانید از این اطلاعات برای اندازهگیری امتیاز OEE در کارخانه یا کارگاه تولیدی خود استفاده کنید و آن را گسترش دهید تا زمانی که آگاهی کامل از OEE هر خط تولید در کارخانه را بدست آورید.
نرمافزار تحت وب مانیتیت با در اختیار داشتن سختافزارهای فوق میتواند دادهها را به صورت مستمر جمعآوری و OEE هر ایستگاه را به طور خودکار محاسبه کند. جهت آشنایی با سختافزار متناسب با ایستگاه کاری خود، دریافت مشاوره رایگان و همچنین استفاده از نسخه دمو با تماس بگیرید.
پرسشهای رایج (FAQ)
دوره زمانی محاسبه OEE چه مدت است؟
تعیین دوره محاسبه تا حدودی به شرایط بستگی دارد و به صورت هفتگی یا ماهانه محاسبه میشود.
آیا زمان صرف شده برای اعمال تغییرات و زمان توقف تجهیزات بر میزان OEE اثر گذار است؟
بله، در مجموع زمان صرف شده بهمنظور تعمیر و نگهداری ماشینآلات، زمان توقف تجهیزات، زمان ناهار بر حاصل OEE موثر است؛ زیرا زمان قابل استفاده برای تولید را از بین میبرند.
تفاوت بین OEE و TEEP چیست؟
OEE معیاری برای ردیابی و بهبود عملکرد تجهیزات در طول زمان استفاده از آنها است. این امر به شناسایی تنگناها و فرصتهای جدید منجر میشود. در حالی که از TEEP برای اندازهگیری عملکرد کلی خط تولید یا چندین قطعه از تجهیزات که هم زمان با یکدیگر کار میکنند، استفاده می شود.
OEE برای کدام صنایع قابل ارزیابی است؟
از OEE میتوان در تمام صنایع و فرایندها اعم از فرایندهای گسسته و پیوسته بهره گرفت.