شش اتلاف بزرگ (MUDA)، اصطلاحی شناخته شده و بسیار مؤثر برای طبقهبندی تلفات ناشی از عدم کارایی تجهیزات در هنگام تولید است. شناخت آنها یکی از چندین ابزار تولید ناب است که تولیدکنندگان میتوانند به کمک آن گلوگاهها را شناسایی و بینش روشن و واضحی از میزان تلفات و هدررفتها به دست آورند. از آنجایی که تمام تولیدکنندگان همواره به دنبال راهی برای افزایش بهرهوری هستند، شناسایی شش ضرر بزرگ یکی از روشهای بهبود اثربخشی کلی تجهیزات (OEE) است که افزایش بهرهوری را به همراه دارد.
۶ اتلاف بزرگ در تولید ناب
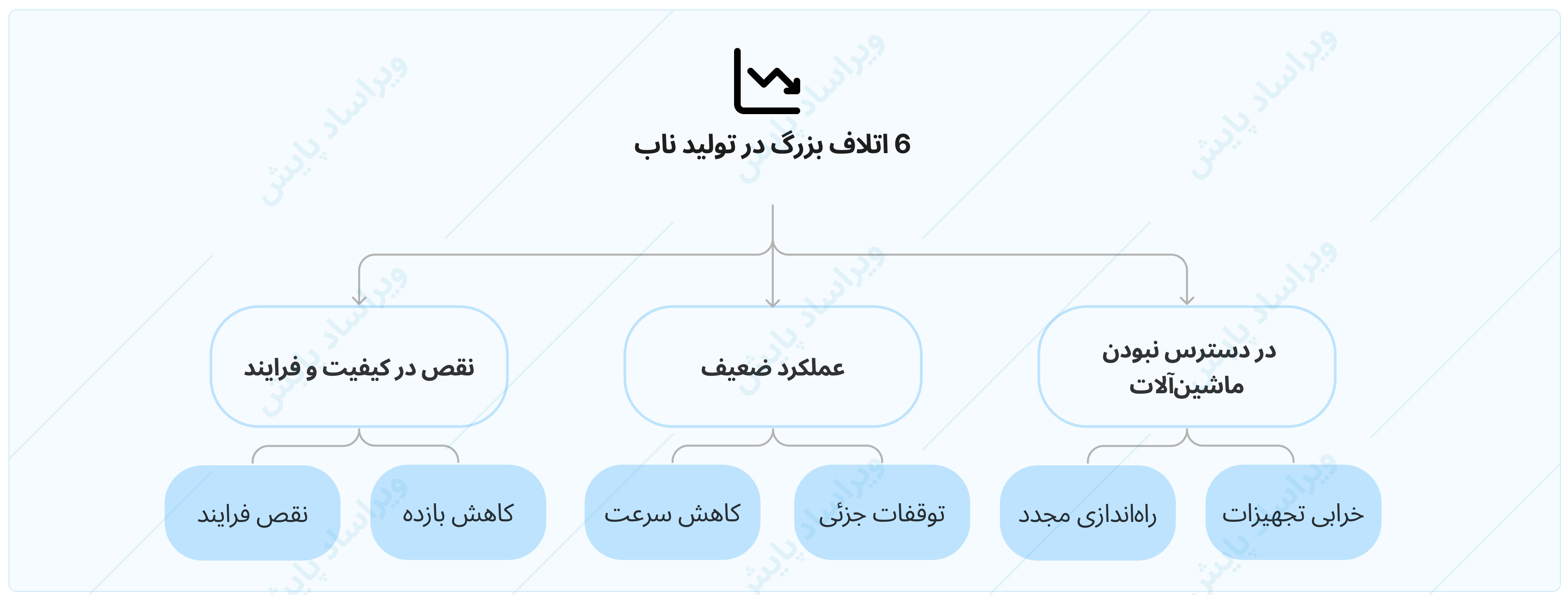
خرابی تجهیزات
خرابی تجهیزات مهمترین منبع توقفهای برنامهریزینشده و بیکاری کارگران است. این امر به دلایل متفاوتی همچون نگهداری نامناسب ماشینآلات، نادیدهگرفتن تعمیرات دورهای و استفاده بیش از حد مجاز از ماشینآلات رخ میدهد و در نتیجه منجر به از کارافتادگی تمام یا بخشی از خط تولید برای مدتی میشود و هزینههای بسیاری را به همراه میآورد.
طولانیشدن تنظیمات و زمان راهاندازی تجهیزات
گاهی اپراتورها بهمنظور اعمال تغییرات جدید مجبور به تعویض قالب و یا تغییر تنظیمات در ماشینآلات میشوند. از آنجایی که انجام کامل این فرایند و همچنین راهاندازی مجدد تجهیزات امری زمانبر است؛ بنابراین مدیران میتوانند به کمک تکنیک SMED (تعویض تک دقیقهای قالب) زمان صرف شده را تا حد امکان کاهش دهند.
توقفهای جزئی
ماشینآلات ممکن است به دلایل مختلفی از جمله گیرکردن تسمه نقاله، مسدودشدن ورودی تجهیزات و تنظیمات نادرست متوقف شوند. معمولا اپراتورها میتوانند این نوع از توقفات را در کمتر از ۱۰ دقیقه برطرف سازند، با اینوجود وقوع توقفات مکرر منجر به کاهش اثربخشی کلی تجهیزات (OEE)، کاهش عملکرد و اتلاف زمان میشود. از اینرو مدیران به دنبال راهی برای حذف یا کاهش توقفات برنامهریزی نشده و همچنین بهحداقلرساندن تمام توقفات برنامهریزی شده هستند، مستندسازی تمام توقفات تنها روشی است که منجر به آگاهی مدیران از فرایندها و شناسایی مسائل پیش از تبدیلشدن به مشکل میشود.
کاهش سرعت
این اتلاف زمانی رخ میدهد که تجهیزات با سرعتی کمتر از سرعت ایدهآل (Cycle Time) مشغول به کار باشند. این امر در نهایت نه تنها منجر به کاهش سرعت تولید میشود بلکه خساراتی همچون باز ماندن از برنامه عملیاتی، تولید کالاهای بیکیفیت، هدررفت سرمایه و افزایش ضایعات را به همراه میآورد. از دلایل رایج کاهش سرعت میتوان به موارد زیر اشاره کرد:
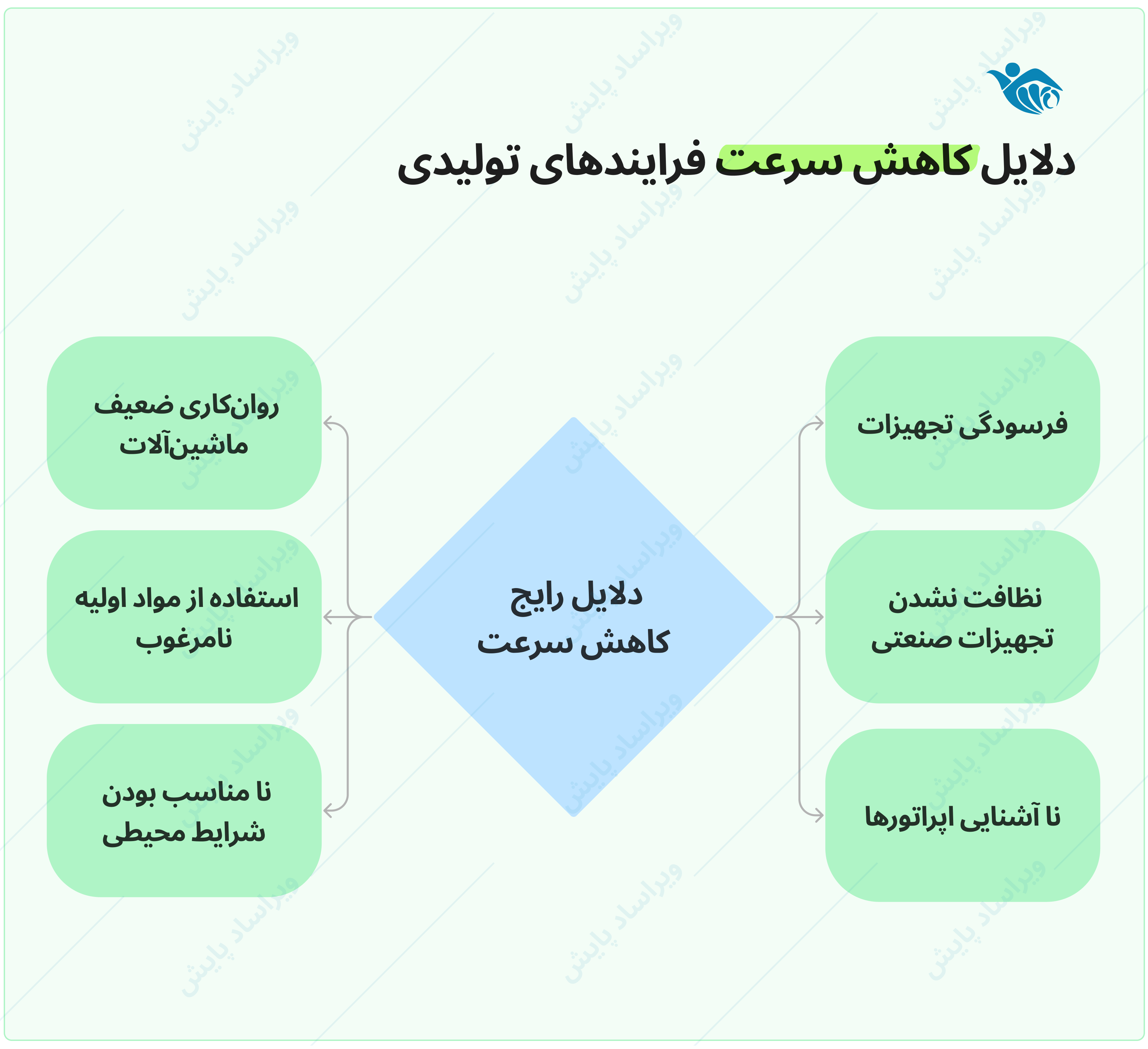
نقص فرایند
نقص فرایند به معنی عدم رعایت استانداردهای لازم و تولید محصولات نامرغوب و بیکیفیت در طول فرآیند تولید است. تنظیم نادرست تجهیزات، خطای اپراتور، و منقضیشدن محصولات دارویی و غذایی مثالهایی از نقص فرایند است که منجر به اتلاف زمان و هزینه میشود. نرمافزار محاسبه OEE با قابلیت کنترل دادههای تولید و شناسایی نقاط ضعف مانع از ایجاد هرگونه نقص در طول فرایند تولید یا مونتاژ میشود.
کاهش کیفیت
تولید محصولات معیوب منجر به کاهش نرخ بازدهی کیفیت میگردد. در بسیاری از مواقع تولید نامرغوب ناشی از وقوع خرابیها در تجهیزات است؛ از اینرو مدیران و اپراتورها میتوانند به کمک سیستم OEE از وجود مشکلات در ماشینآلات مطلع شوند و سپس اقدامات لازم جهت بهبود کیفیت و افزایش بازده عملیاتی را انجام دهند.
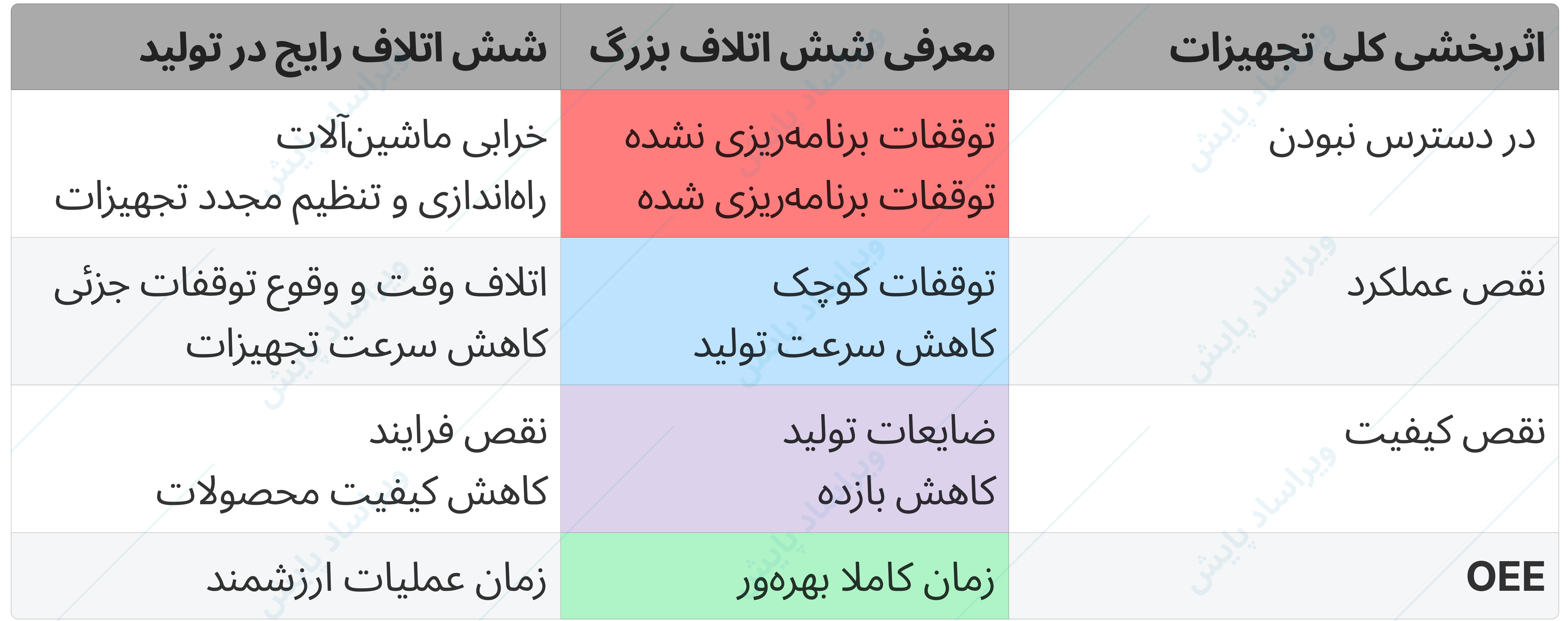
اهمیت شناسایی انواع اتلاف در تولید ناب
شناسایی و ثبت شش ضرر بزرگ در کسبوکارها بینش دقیقی در مورد عوامل موثر بر OEE (در دردسترسبودن، عملکرد و کیفیت) ارائه میدهد. همچنین با در اختیار گذاشتن اطلاعات ارزشمند درباره نحوه انجام فرایندها منجر به بهبود بهرهوری و کاهش هزینهها میشود و در هنگام روبهرو شدن با مشکلات به تولیدکنندگان کمک میکند تا تصمیمگیری اثربخش و به موقعی را اخذ نمایند.
مزایای شناسایی اتلافهای تولید
شناسایی شش ضرر بزرگ، در مدت کوتاهی اطلاعات مفیدی درباره چگونگی انجام فرایندهای تولید و همچنین همسو بودن یا نبودن آن با شاخص OEE را در اختیار مدیران میگذارد، از سویی دیگر تمرکز بر به حداقل ساندن اتلافات ناشی از شش ضرر بزرگ برای ماهها منجر به توانمندی مدیران و تولیدکنندگان در انجام اقدامات لازم و مؤثر در جهت بهبود تولید و افزایش بهرهوری میشود.
چگونه شش ضرر بزرگ را تجزیهوتحلیل کنیم؟
اولین قدم برای تجزیهوتحلیل شش اتلاف بزرگ، درک تأثیر هر یک از اتلافها بر عملکرد خط تولید است. ابزارها و تکنیکهای مختلفی مانند نمودارهای پارتو، نمودارهای استخوان ماهی و تکنیک ۵ چرا میتوانند با اولویتبندی مهمترین ضررها، تولیدکنندگان را در ایجاد راهکارهای مناسب یاری کنند.
قدم بعدی، اندازهگیری میزان OEE و مقایسه آن با تولید ایدهآل است. به عبارتی دیگر؛ هرچه تفاوت بین عملکرد واقعی و ایدهآل بیشتر باشد، کارخانه از اهداف خود دورتر است. در این روش تولیدکنندگان میتوانند با شناسایی و تعیین معیارهای عملیاتی، تولید را در جهت تحقق اهداف پیش ببرند.
نحوه شناسایی و حذف اتلاف در تولید ناب
گرچه بهطورکلی نمیتوان باعث حذف کامل اتلافها شد؛ اما در اینجا روشهایی را به شما معرفی میکنیم که منجر به کاهش چشمگیر اتلافها میشود.
نظارت بر فرایندهای تولید
تولیدکنندگان میتوانند با نظارت بر فرایند تولید از تمام رویدادهای تولید مطلع شوند، همچنین گلوگاهها و نقاط ضعف را شناسایی کنند و اقدامات لازم را بهمنظور بهبود فرایندها به کار گیرند. مانیتورینگ سریعترین روش برای بهبود توان عملیاتی و سودآوری است.
روبهروشدن با مشکلات
انجام فرایند تولید تنها زمانی منجر به سودآوری میشود که باهدف رفع نیاز مشتری صورت گیرد، در غیر این صورت انجام هر فرایند برابر است با ضرر و زیان کارخانه. نرمافزار هوشمند مانیتیت به مدیران امکان میدهد تا با بررسی تاریخچه تولید و نظارت بر دادهها تمام فرایندهای ضررده را شناسایی کنند و سپس کارخانه را به سوددهی برسانند.
سنجش زمان بین دو اتلاف
یکی دیگر از روشهای کاهش اتلاف، نظارت و اندازهگیری زمان بین دو اتلاف است. به عبارتی دیگر؛ مدیران و اپراتورها میتوانند زمان بین آخرین فرایند ایدهآل تا اولین فرایند ایدهآل بعدی را اندازهگیری و محاسبه کنند، سپس اقدامات لازم برای کاهش این زمان را انجام دهند.
جمعآوری خودکار دادهها
نرمافزار مدیریت تولید یکی از ابزارهای هوشمندی است که به کمک سخت افزارهای اتوماتیک میتواند با جمعآوری دادههای دقیق و بررسی آنها مانع از وقوع بسیاری از توقفات در هنگام تولید شود. این سیستم با ثبت دقیق تمام توقفات اعم از توقفات برنامهریزی شده و برنامهریزی نشده، توقفات کوچک و حتی زمان استراحت کارگران و همچنین مقایسه آنها بین شیفتهای مختلف، تولیدکنندگان را در تحلیل توقفات و کاهش زمان آنها یاری میکند.
اگر شما نیز بهدنبال حذف روشهای سنتی برای جمعآوری دادهها هستید، کلیک کنید.
جلوگیری از اتلاف در تولید ناب به کمک سیستم مانیتیت
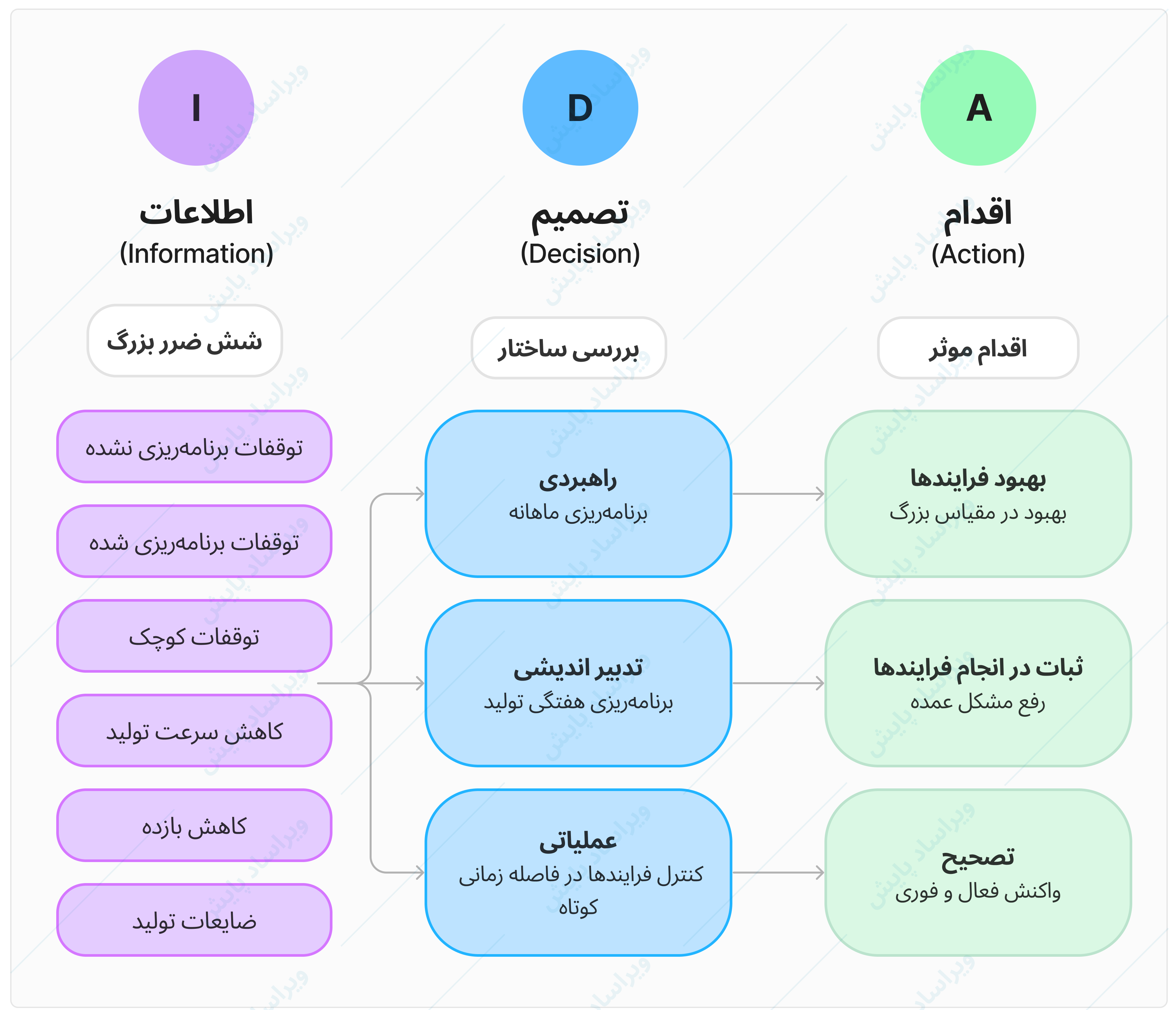
سیستم مدیریت تولید مانیتیت با قابلیت جمعآوری دادههای هوشمند تولیدکنندگان و مدیران را در شناسایی مشکلات و خطاها یاری میکند و همچنین به بررسی فرایندها میانجامد و مانع از تولید ضایعات و ایجاد توقفات پیدرپی در کارخانه میشود. یکی دیگر از مزایای بهکارگیری نرمافزار مانیتیت امکان نظارت بر فرایندهای تولید و دسترسی به ابزارهای متفاوت است که داشبوردهای تخصصی را در اختیار تولیدکنندگان میگذارد تا با استفاده از روشهای متکی بر هوش مصنوعی فرایندهای تولید را بهینه و کارآمد سازند.